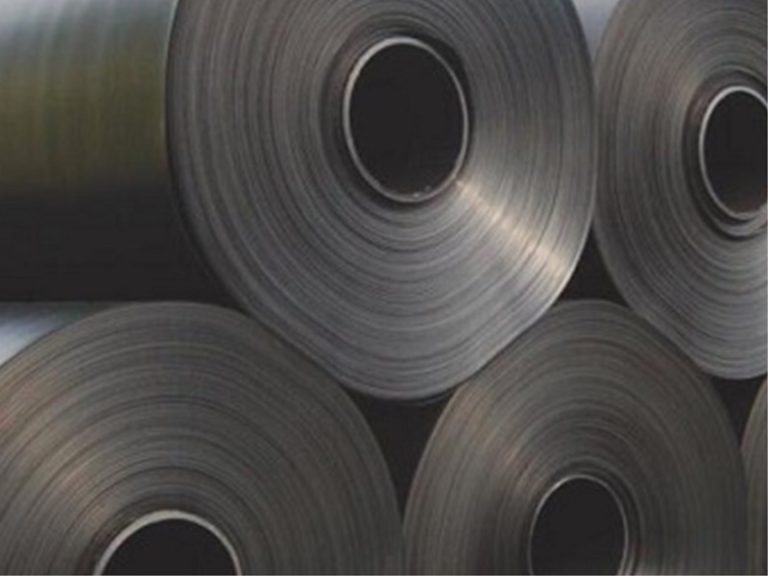
در این مقاله یک بررسی کامل در مورد آسیبهای فیزیکی، فرآیندهای تخریب مواد و ایجاد سوراخ در ورق ژئوممبران توسط ریزترکها انجام شده است. به نظر میرسد که آزمونهای محل نشت الکتریکی Electrical Leak Location (ELL) به عنوان ابزاری مؤثر در شناسایی سوراخهای ایجاد شده در اثر آسیب فیزیکی در هنگام نصب ورق و دفن زباله و کمک به تعمیر آنها است. تخریب ورق HDPE با شرایط نوع در معرض بودن آن ورق، انرژی فعالسازی فرآیند تخریب آنتی اکسیدانی و مقاومت اکسیداتیو مواد کنترل میشود. در مواردی که ورق تحت تنشهای طولانی مدت قرار دارد، به وجود آمدن ریزترکها منجر به ایجاد سوراخ میشود و با شروع اکسیداسیون ورق، سرعت ترک خوردگی افزایش مییابد. در این مقاله همچنین در مورد روشهای به حداقل رساندن و تاخیر در افزایش سوراخها بحث شده است.
مقدمه
قانونی اخیراً در انگلستان معرفی شده است که دولت را موظف میکند تا آبهای زیرزمینی را در برابر آلودگی محافظت کند و در صورت لزوم اصلاحاتی برای آن انجام دهد. اگرچه بسیاری از مشکلات فنی طراحی محلهای دفن زباله از دیرباز وجود داشته است، اما نحوۀ نظارتی جدید به گونهای است که درک کمّی از طراحی محلهای دفن زباله و کنترل شیرابهها را با اولویت بسیار بالاتری در آژانس حفاظت از محیط زیست پیگیری میکند. این امر به ویژه زمانی که آبهای زیرزمینی حساس باشد یا گاز دفن زباله خطری برای مردم محلی ایجاد کند اهمیت دارد. بسیاری از لندفیلهای مدرن از ژئوممبرانهای مصنوعی، که به طور معمول از HDPE ساخته شده اند، به عنوان بخشی از یک سیستم آستری در پایه استفاده میکنند. HDPE مانع جریان و حرکت مایعات است و رد شدن از ورق HDPE محدود به فرآیندهای نفوذ مولکولی است، که معمولاً بسیار کند هستند. با این وجود، در محیط دفن زباله، فاکتورهای دیگری ازجمله کیفیت نصب، تنشهای ناشی از بیثباتی به خاطر شیب، تماس ورق با مواد شیمیایی خورنده و تقلیل آنتی اکسیدانهای ورق در طول زمان ممکن است روی خواص HDPE تأثیر بگذارد، که میتواند نقایصی را ایجاد کرده یا باعث خرابی شود.
در یک مقاله بررسی کاملی از فرآیندهای تخریب ژئوممبران پلی اتیلن و تناوب نقصها انجام شده است [۱]. نتایج آن مبنایی را فراهم میکند که راهنماییها و فرضیات مربوط به عملکرد محل دفن زبالهها در میان مدت تا طولانی مدت، بتواند تدوین شود.
مطالعات شیمی شیرابههای دفن زباله و فرآیندهای تخریب ژئوممبران نشان میدهد که برای از بین رفتن محلهای دفن زباله با استفاده از روشهای فعلی به طور معمول صدها سال (اگر نه هزاران سال) زمان نیاز خواهد بود. تنها پس از گذشت این دوره این زباله ها دیگر خطر آلودگی برای محیط اطراف خود نخواهند داشت. بنابراین پایداری مهار مهندسی شده و اقدامات کنترلی در ارزیابی آلودگی بالقوه در دراز مدت حیاتی است.
طول عمر ورق ژئوممبران
طول عمر یک ورق ژئوممبرانی را میتوان مدت زمانی تعریف کرد که ورق به عنوان یک مانع موثر هیدرولیک برای اهداف محل مورد نظر عمل خواهد کرد. واضح است که این امر به شرایط موجود در محل و برای کیفیت آب زیرزمینی، میزان قابل قبول نشت آلایندههای خاص بستگی دارد. عوامل اصلی مؤثر بر این موارد عبارتند از:
- تعداد و اندازه سوراخها در یک ورق ژئوممبران در معرض شیرابه؛
- نوع ورق (تک لایه، کامپوزیت، و یا دو لایه)؛
- در یک ورق کامپوزیتی، کیفیت تماس در سطح مشترک ماده معدنی و ژئوممبران.
- تداوم منبع شیرابه (به عنوان مثال نرخ کاهش غلظت منبع)
- نوع منبع شیرابه و ذات و غلظت آلایندهها در شیرابه؛
- حساسیت محل نسبت به کیفیت آب زیرزمینی (به عنوان مثال آسیب پذیری های آب زیرزمینی).
یک ورق ژئوممبران ممکن است دارای تعداد مشخصی سوراخ با طیفی از اندازه باشد. در یک محل نشت حاصل ممکن است قابل قبول در نظر گرفته شود اما در یک مکان حساس تر، ممکن است همین نشت غیر قابل قبول تلقی شود. از این رو میتوان نتیجه گرفت که ایجاد سوراخ در ورقهای ژئوممبران، که با مکانیسمهای آسیب فیزیکی، ریزتَرَکها یا تخریب مواد سازنده ایجاد شده، تنها یکی از عوامل پیش بینی طول عمر آن ورق است.
بیشتر بخوانید : ژئوتکستایل چیست؟
آسیب فیزیکی
بیشترین آسیب به ژئوممبران، که باعث ایجاد سوراخ یا نقص نامحسوس میشود، در حین نصب و درزگیری ورق و در نتیجۀ قرار دادن زهکشی پوششی یا مواد پوشاننده رخ میدهد. اکنون دلایل آسیب ژئوممبران بطور گستردهای از نتایج آزمون محل نشت الکتریکی (ELL) بدست میآیند. این آزمونها با استفاده از سیستمهای ثابت و متحرک ELL انجام میشود. آزمونهای متحرک ELL بعد از اتمام ساخت آستر و پس از قرار دادن مواد پوششی انجام میشوند، اما قادر به شناسایی سوراخها پس از شروع دفن زباله نیستند. آزمونهایی که از سیستمهای ثابت (یا دائمی) ELL استفاده میکنند، میتوانند در هر زمان پس از نصب سیستم نیز انجام شوند و به خوبی در مراحل عملیاتی و پس از بسته شدن لندفیل ادامه یابند. در جایی که آزمونهای ELL انجام نشود، باید انتظار انواع سوراخ شناسایی شده در این ورقها وجود داشته باشد. دادههای کمی به طور خاص روی شناسایی سوراخهای یافت شده توسط آزمونهای ثابت ELL پس از شروع دفن زباله منتشر شده است. نوسکو و همکاران (۱۹۹۶) گزارش دادند که تنها ۲% از کل سوراخهای شناسایی شده در مرحلۀ پس از ساخت و ساز و در هنگام پر کردن زباله رخ داده است [۲].
دادههای یک شرکت آزمون ELL در مورد آزمونهای ثابت ELL که در ۱۷ سایت تجاری با مساحت حدود ۸۰۰۰۰۰ متر مربع انجام شده، مورد بررسی قرار گرفته است. حداکثر دوره نظارت بر نشت پس از نصب ورق ۶سال بود. از سوراخهای کشف شده، ۴۲% در حین فعالیت سایت رخ داده، که نسبت بسیار بیشتری از ۲% پیدا شده توسط نوسکو و همکارانش است. برای سوراخهای ایجادشده در مرحلۀ عملیاتی، دلایل مربوط به آسیب فیزیکی بوده است؛ نه از بین رفتن مواد سازندۀ ورق ژئوممبران. همچنین نتایج یک شرکت آزمون ELL دیگر که از آزمون سیستمهای ثابت ELL طی دوره ۷ ساله ۱۹۹۶-۲۰۰۳ استفاده کرده نیز مورد بررسی قرار گرفته است. داده ها از ۸۸ سلول و ۱۸ محل تجمع شیرابه در ۵۵ سایت دفن زباله در شرق اروپا، بلژیک و انگلستان به دست آمده است. مساحت کل مورد بررسی تقریباً ۱٫۰۲۲٫۰۰۰ متر مربع بود. تعداد نواقص بزرگ ۱۴۶۰ عدد بود که ۷۴٪ از آن در بررسی نشت اولیه در انتهای ساخت و ساز و ۲۶٪ در بررسیهای بعدی مشاهده شده است. شایع ترین علت آسیب مشاهده شده در بررسیهای ثانویه (۷۸٪)، سوراخ شدگی با سنگ است، که از رفت و آمد بر روی سلولهای خالی ناشی شده بود. هیچکدام از خسارتها به عدم دوام مواد ژئوممبران نسبت داده نشده است.
نظارت گسترده در یکی از سایت های دفن زباله در انگلستان از سال ۱۹۹۵ تاکنون موارد دیگری را نیز آشکار کرده است:
- ۲۷% از نقصها پس از اتمام نصب ورق عایق شناسایی شده است (یعنی یا قبل از دورۀ شروع دفع زباله در سلول یا پس از شروع دفن زباله در لندفیل).
- تنها دو سوراخ به دلیل موقعیت غیرقابل دسترسشان، در ورق تعمیر نشده باقی ماندند و هیچ نشت قابل ردیابی توسط سیستم ELL مشخص نشده است.
- اندازه سوراخهای یافت شده پس از اتمام ورق در محدودۀ سوراخهای با سایز یک پین تا پارگی های بزرگ ناشی از حرکت گیاهان متغیر بود.
- تقریباً تمام سوراخهای جدید کشف شده پس از شروع دفع زباله ناشی از فعالیتهای اولیه دفن زباله (به عنوان مثال سوراخ شدن توسط اشیاء درون زباله و حرکت گیاهان) است.
- بررسیهای متناوب سه ماهه، باعث شناسایی زودهنگام نقصها و ترمیم آنها شد.
- هیچ مدرکی مبنی بر پیشرفت تدریجی سوراخها وجود ندارد.
دوام ورق ژئوممبران
اکسیداسیون حرارتی عاملی است که بیشترین اثر نامطلوب را در روند تخریبی ژئوممبران HDPE دفن شده دارد. اکسیداسیون وابسته به دما است؛ بدین صورت که با افزایش دما اکسیداسیون به سرعت افزایش مییابد. با پیشرفت اکسیداسیون، خصوصیات فیزیکی و مکانیکی پلیمر شروع به تغییر میکند که در نهایت منجر به ناکارآمدی ژئوممبران به عنوان یک مانع هیدرولیک مؤثر میشود. اکسیداسیون پلی اتیلن با افزودن تثبیت کنندههای مناسب به رزین مانند آنتی اکسیدان های مختلف که با مختل کردن واکنشهای مختلف اکسیداسیون کار میکنند، به تأخیر میافتد. انواع مختلفی از آنتی اکسیدانها وجود دارد که از پلیمر به روشهای مختلف و در محدودههای مختلف دمایی محافظت میکنند. به همین خاطر مجموعهای از آنتی اکسیدانها به ژئوممبران HDPE اضافه میشوند تا طیف گسترده ای از مقاومت اکسیداسیونی را هم در طول روند ساخت و هم افزایش عمر مواد فراهم کند.
در مقاله ای تخریب اکسیداسیون پلی اتیلنها در کنار تثبیتکنندههای آنتی اکسیدانی به عنوان یک فرآیند سه مرحله ای شرح داده شده است [۳]. مرحله اول کاهش آنتی اکسیدانها است که یا ناشی از مصرف آنها در اثر واکنشهای شیمیاییست؛ و کاهش فیزیکی آنها بخاطر استخراج [از ورق] یا فراریت است. واکنشهای اکسیداسیون سپس در یک دوره القایی اولیه بسیار آهسته شروع میشود که طی آن تخریب خود ژئوممبران در کمترین سطح مشاهده میشود. سپس در مرحلۀ نهایی، اکسیداسیون باعث از بین رفتن میزان قابل توجهی از خواص مواد میشود.
همچنین در گزارش های دیگری از بررسی طولانی مدت روی اکسیداسیون ژئوممبرانها، عوامل متعددی بخاطر تأثیر عمدهشان روی نتایج آزمون فرسودگی آزمایشگاهی و همچنین پایداری طولانی مدت ژئوممبرانها شناسایی شده است:
- خواص رزینهای HDPE {مواد سازنده} و مجموعۀ آنتی اکسیدانهای استفاده شده؛
- مدت زمان آزمون؛
- محیطی که نمونه در معرض آن قرار میگیرد مانند هوا، آب، شیرابه یا خاک (اشباع و خشک)؛
- در دسترس بودن اکسیژن در کنار ورق.
- دماهای آزمون فرسودگی؛ و،
- انرژی فعالسازی فرآیند مصرف آنتی اکسیدان.
انرژی فعالسازی (Ea) نشان دهندۀ حداقل انرژی لازم در فرآیند مصرف آنتی اکسیدان است و به خواص رزین HDPE، آنتی اکسیدانهای مورد استفاده و شرایط محیطی که در آن آنتی اکسیدان از بین میرود بستگی دارد. از آنجا که میزان کاهش آنتی اکسیدان به صورت تصاعدی وابسته به انرژی فعالسازی است، استفاده از مقدار مناسب {ماده} در تخمین زمان کاهش آنتی اکسیدان مهم است، اما یافتن چنین مقادیری کمی دشوار است.
سه تیم مختلف به کمک آزمون زمان القای اکسیداسیون (Oxidative Induction Time (OIT طبق استاندارد (ASTM D3895) نرخ کاهش آنتی اکسیدانها را در ژئوممبرانهای مختلف، شرایط محیطی متفاوت و دماهای مختلف فرسودگی تعیین کردند که در شکل ۱ قابل مشاهده است.
شکل ۱ – مقایسۀ نرخهای کاهش آنتی اکسیدان بر طبق تحقیقات تیمهای مختلف
از مقایسۀ این نتایج میتوان گفت که:
- کاهش دمای قرار گرفتن محیطی که ژئوممبران در معرض آن قرار دارد باعث کاهش چشمگیر نرخ کاهش آنتی اکسیدان میشود.
- غوطه وری در شیرابۀ سنتزی نرخ کاهش آنتی اکسیدانی بسیار بالاتری نسبت به سایر بسترها به همراه داشت.
- آزمایشی که با مدت طولانی تر توسط مولر و جیکوب در سال ۲۰۰۳ انجام شد یک روند کاهشی دومرحلهای را نشان داد که در آن، مرحلۀ دوم بسیار کند است.
مقادیر بالای OIT اولیۀ با پایداری طولانی مدت در برابر اکسیداسیون مرتبط نیست. آنتی اکسیدانهای خاص به میزان قابل توجهی مقدار OIT اولیه را افزایش میدهند، اما در زیر دمای ۱۵۰ درجه سانتیگراد بی اثر هستند و به پایداری طولانی مدت در برابر اکسیداسیون در دمای عملیاتی کمکی نمیکنند. بنابراین، خواص ژئوممبران پلی اتیلنی باید نه تنها مقدار اولیۀ OIT را تصریح کند، بلکه همچنین نیاز به حفظ حداقل مقدار OIT بر طبق یک آزمایش فرسودگی استاندارد دارد [۴].
این مدل آزمایشی کاهش آنتی اکسیدان /انرژی فعالسازی برای هر فرمولاسیون ژئوممبران بستگی به ترکیب واقعی مجموعۀ آنتی اکسیدانی مورد استفاده و خواص رزین پلی اتیلن سازنده دارد.
دوام تخمینی(سال) | انرژی فعالسازی(kj/mol) | میانگین دمای ورق( C ) |
۴۵۰-۶۵۰ | ۶۰ | ۲۰ |
۹۰۰-۱۳۰۰ | ۷۰ | ۲۰ |
۱۴۰-۲۰۰ | ۶۰ | ۳۵ |
۲۲۰-۳۲۰ | ۷۵ | ۳۵ |
۳۷۰-۵۳۰ | ۸۰ | ۳۵ |
۴۶-۶۶ | ۶۰ | ۵۰ |
۶۴-۹۱ | ۷۰ | ۵۰ |
پایداری و دوام را با محصولات ژئوگرید تجربه کنید
جدول ۱ – برآوردهای دوام ورق ژئوممبران HDPE (تا زمان اتمام آنتی اکسیدان) در شرایط دفن زباله در پروژههای تحقیقاتی آزمایشگاهی
با استفاده از نرخ کاهش OIT حاصل از این رویکرد، میتوان تخمینی از دوام مواد ورق ژئوممبران را از معادله آرنیوس در وابستگی دمایی فرآیند کاهش آنتی اکسیدان بدست آورد [۳]. نتایج حاصله برای میانگین دمای متوسط ورق و انرژی فعالسازی که در جدول ۱ آورده شده، تأثیر بسیار شدید درجۀ حرارت ورق را بر میزان کاهش آنتی اکسیدان و دوام ورق HDPE نشان میدهد.
این تخمین دوام فقط به مصرف کامل آنتی اکسیدانها مربوط میشود و به طور مستقیم با توانایی دوام عملی ورق ژئوممبرن به عنوان یک مانع هیدرولیک مؤثر ارتباطی ندارد.
شرایط محیطی که ژئوممبران در معرض آن قرار میگیرد
دمای یک ورق پلی اتیلنی دفن شده، تاثیر کنترلکنندهای روی نرخ تخریب آن دارد. در یک پژوهش در سال ۱۹۹۸ که روی دمای لندفیل ها صورت گرفت نشان داده شد که همبستگی روشنی میان دما در زیر لندفیل و شیرابههای روی آن وجود دارد (شکل ۲).
شکل ۲ – نسبت دماهای زیر لندفیل با شیرابۀ روی آن
ژئوممبران HDPE مقاومت شیمیایی بسیار خوبی در مقابل شیرابه های ناشی از زبالههای شهری، صنعتی و تجاری در محل های دفن زباله در انگلستان از خود نشان دادند.
ایجاد ریزترک ها در اثر تنش
ایجاد ریزترک ها در اثر تنش در ژئوممبران HDPE به خوبی گزارش شده است. منحنیهای نرمال ترکخوردگی در اثر تنش که با استفاده از آزمون ترک خوردگی در اثر تنش NCTL (ASTM D5397) بدست میآید، حالت های شکست چقرمه و شبهتُرد را نشان میدهد که در آن شکست در شیب (یا زانو) معرف نقطۀ انتقال چقرمه/تُرد است. در تحقیقاتی روی دوام ورق در آلمان در سال ۱۹۹۰، یک روند سه مرحلهای (شکل ۳) مشخص شد که در آن منحنیها در دماهای آزمونی مختلف، یک زانو {یا شکست} دوم را نشان میدادند که به دنبال آن یک شیب یکنواخت تقریبا عمودی وجود داشت (مرحلۀ سوم). زانوی دوم به عنوان مرحله ای که تمام آنتی اکسیدانها مصرف شدهاند در نظر گرفته شده و پس از آن هرگونه فشاری باعث ترک خوردگی میشود.
شکل ۳ – منحنی شکست سه مرحله ای به عنوان عملکردی از دما
محصولات ژئوسنتتیک،بهترین انتخاب برای پروژههای شگفتانگیز
بنابراین، هنگامی که یک ژئوممبران همزمان با وقوع اکسیداسیون در معرض تنش است، روند تخریب پیچیده تر از مدلهای ساده ای است که در مطالعات آزمایشگاهی روی نمونههای بدون تنش انجام میشود. حتی هنگامی که آنتی اکسیدانها به طور کامل مصرف میشوند و اکسیداسیون شروع میشود، ورق ژئوممبران به عنوان یک مانع هیدرولیک موثر در جای خود باقی میماند، مگر اینکه آسیب فیزیکی در آن رخ دهد یا سوراخی روی آن ایجاد شود. با در نظر نگرفتن آسیبهای فیزیکی، سوراخها در ورق بایستی در نتیجۀ ترک خوردگی در اثر تنش ایجاد یا بزرگ شوند، مگر اینکه تنش یا فشار به حدی باشد که باعث شکست چقرمۀ کششی شود.
عمر ورق ژئوممبران به محض بروز نشتی بیش از حد آن در سایت، پایان مییابد. اگر آسیبهای فیزیکی بتواند به میزان قابل قبولی محدود شود، عمر ورق به عنوان یک مانع هیدرولیک مؤثر، به توسعۀ ترکخوردگی تحت تنش در مکانهایی بستگی خواهد داشت که باعث میشود نشت بیش از حد رخ دهد.
مراحل ایجاد سوراخ در ورق ژئوممبران
مرحلۀ اول: تعیین تعداد و سایز سوراخهای ایجادشده پس از نصب و اعمال مادۀ پوششی؛ که با یک آزمون ELL مناسب میتوان مقدار آن را تا صفر یا حداقل سوراخ تقلیل داد.
مرحلۀ دوم: این مرحله در مورد سوراخ هایی است که قبل یا در حین عملیات های تخلیۀ زباله در سایت بر اثر مکانیسمهای آسیب فیزیکی که باعث ایجاد سوراخ های جدید یا بازشدن نقصها میشود. با وجود یک سیستم ELL ثابت میتوان این سوراخ ها را شناسایی و تعمیر کرد.
مرحلۀ سوم: شواهد موجود نشان از عدم توسعه یا ایجاد سوراخها تا حداقل ده سال پس از تکمیل لندفیل دارند. به علت عدم وجود عامل ایجاد سوراخ، منطقی است که طول مرحلۀ سوم را بین ۱۰ تا ۵۰ سال در نظر گرفت. طول این دوره توسط عواملی مانند خواص مواد سازنده، درجۀ تاثیر محافظت از ورق، کیفیت طراحی و نصب استاندارد آن تحت تاثیر قرار میگیرد.
مرحلۀ چهارم: این مرحله نمایانگر دورۀ اصلی کاهش آنتی اکسیدانها بوده و شامل مرحلۀ آغازین القایی اکسیداسیون است. همچنین در این مرحله ترکخوردگی بر اثر تنش نیز به صورت گرادیانی افزایش مییابد.
مرحلۀ پنجم: این مرحله زمانی اتفاق میافتد که اکسیداسیون ورق ژئوممبران آغاز میشود. در این صورت ژئوممبران شکننده شده و آسیب ترک خوردگی بر اثر تنش در سرتاسر مکانهایی که ورق تحت تنش است با سرعت بیشتری انجام خواهد شد.
مرحلۀ ششم: پیشبینی میشود که تولید یا گسترش بیشتر سوراخها در ژئوممبران با سرعت کمتری ادامه پیدا کند. ژئوممبران به یک مانع تجزیه شدۀ «دارای نشتی» تبدیل میشود و برای همیشه غیرفعال باقی میماند.
منابع
- Environment Agency, 2004. The likely medium to long-term generation of defects in geomembrane liners. R&D Technical Report P1-500/1/TR. EA, Bristol.
- Nosko, V., Andrezal, T., Gregor, T., Ganier, P., 1996. SENSOR Damage Detection System (DDS) — the unique geomembrane testing method. In: De Groot, M.B., den Hoedt, G., Termaat, R.J. (Eds.), Geosynthetics: Applications, Design and Construction. Proc., 1st
- Hsuan, Y.G., Koerner, R.M., 1995. Long-term durability of HDPE geomembranes. Part I — depletion of antioxidants. GRI Report, vol. 16. Geosynthetics Institute.
GRI GM13, 2003. Standard specification for test properties, testing frequency and recommended warrant for high density polyethylene (HDPE) smooth and textured geomembranes. Rev., vol. 6. Geosynthetics Research