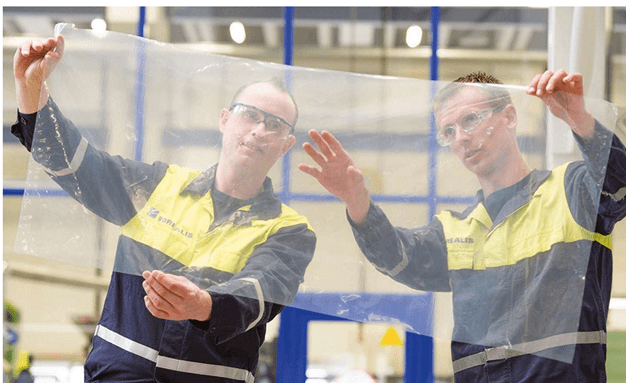
پلی اتیلن به عنوان پر مصرف ترین پلیمر در جهان شناخته شده که بیش از ۳۲% از کل پلاستیک تولیدی ( بیش از ۹۰ میلیون تن ) را شامل می شود[۱و۲]. عمده مصرف این دسته از مواد در بسته بندی، ورق های ژئوممبران و ظروف نگهدارنده می باشد[۱]. در ساده ترین ساختار مولکولی، زنجیر ها شامل تعداد زوج CH۲ بوده که با پیوند کوالانسی به یکدیگر متصل شده اند (شکل ۱). با تغییر در شاخه های جانبی، گرید های مختلف پلی اتیلن تولید می شود که در خواص فیزیکی و مکانیکی متفاوتند.
HDPE
پلی اتیلن سنگین بدلیل نسبت مقاومت به چگالی بالا از اهمیت بالایی برخوردار است. با توجه به پایین بودن درصد شاخه ها و همچنین کوچک بودن آنها، میزان بلورینگی در آن بالا و در نتیجه چگالی آن در محدوده g/cm۳ 97/۰ – ۹۴/۰ قرار می گیرد. از طرفی بلورینگی بالا در این پلیمر باعث افزایش سفتی و کاهش نفوذ پذیری می شود، از این رو در مواردی نظیر ورق ژئوممبران HDPE ، ظروف بسته بندی، پوشش محل های دفن زباله و لوله های پلی اتیلنی مورد استفاده قرار می گیرد.
UHMWPE
پلی اتیلن با وزن مولکولی بسیار بالا، با توجه به داشتن خواص مکانیکی مناسب، طول عمر بالا و سازگاری با بدن انسان، در تولید زانو، آرنج و دیگر اتصالات استخوانی بدن مورد استفاده قرار می گیرد. همچنین به روش قالبگیری فشاری و رم اکسترودر، می توان ورق و میله تولید کرد. طبق استاندارد ISO پلی اتیلن هایی با وزن مولکولی بزرگتر از ۱،۰۰۰،۰۰۰ و طبق استاندارد ASTM پلی اتیلن با وزن مولکولی بزرگتر از ۳،۵۰۰،۰۰۰ در دسته بندی UHMWPE قرار می گیرد[۴].
MDPE
پلی اتیلن با وزن مولکولی متوسط در حقیقت مخلوطی از HDPE و LDPE می باشد، در نتیجه خواصی مشابه این دو پلیمر ارائه می دهد. در مواردی که مقاومت ضربه بالا، حساسیت به Notch پایین مد نظر باشد مورد استفاده قرار می گیرد. در مقایسه با HDPE مقاومت به Creep بالاتر ولی سختی پایین تری دارد، از این رو در لوله و اتصالات گاز و فیلم های بسته بندی مورد استفاده قرار می گیرد[۵].
روش های پلیمریزاسیون:
با توجه به شرایط فرآیندی نظیر دما، فشار و کاتالیست، نوع و درصد کومونومر انواع مختلف پلی اتیلن تولید می شود. به منظور دستیابی به پلی اتیلن سبک، از راکتور های با فشار و دمای بالا استفاده می شود. همچنین استفاده از کاتالیست های زیگلر- ناتا و متالوسنی به منظور سنتز پلی اتیلن سبک خطی و پلی اتیلن سنگین ضروری می باشد. در این شرایط، فرآیند در دما و فشار پایین تری نسبت به سنتز پلی اتیلن سبک انجام می شود.
پلی اتیلن سبک LDPE:
در فرآیند تولید پلی اتیلن سبک (شکل ۷)، گاز اتیلن a، که ۲۰-۱۰ درصد ورودی را تشکیل میدهد، با گازهای b, c که از محصول خروجی بازیافت شده اند وارد کمپرسور ۱ شده و به فشار psi 1500-4000 می رسد. گاز فشرده شده با رسیدن به فشار psi 22500-15000 در کمپرسور ۲، با آغازگر و عامل انتفال به زنجیر در راکتور ۳ مخلوط می شود. پلی اتیلن نهایی در دو مرحله فشار بالا و فشار پایین از روغن، واکس و اتیلن جدا شده و پس از ورود به اکسترودر ۹ به عنوان محصول نهایی به شکل گرانول خارج می شود.
از دیدگاه مورفولوژی، زنجیرهای پلی پروپیلن در دو فاز کریستال و آمورف قرار می گیرند که فاز آمورف قسمت های کریستال را به یکدیگر متصل می کند. تحت تاثیر شرایط فرآیندی، درصد فاز کریستال و آمورف متفاوت می شود. از طرفی مواد اولیه مورد استفاده نیز تاثیر به سزایی در مورفولوژی نهایی محصول دارد[۸]
به طور کلی پلی پروپیلن به عنوان پلیمری مهندسی با قیمت پایین شناخته می شود. در مقایسه با پلی اتیلن از سفتی بالاتر، دانسیته کمتر، مقاومت دمایی بالاتر ( در شرایط بدون تنش مکانیکی ) برخوردار است. از طرفی به طور کلی، مقاومت خستگی بالا، مقاومت شیمیایی مناسب، مقاومت به رشد ترک بالا در کنار فرآیند پذیری مناسب از طریق تزریق و اکستروژن، ویژگی های مناسب پلی پروپیلن می باشند.
در مقابل خواصی نظیر کاهش حجم ( shrinkage)، مقاومت ضربه، مقاومت اکسیداسیون و UV و مقاومت Creep پایین، نقاط ضعف پلی پروپیلن می باشند. به همین منظور، با استفاده از برخی افزودنی ها نظیر تالک و EPDM خواص PP را بهبود می دهند[۷].
بیشتر بخوانید: ژئوممبران EPDM چیست؟
از پلی پروپیلن در مصارف متعددی نظیر تولید ورق، الیاف بافته ( نظیر فرش ) و الیاف نبافته نظیر ژئوتکستایل، نوار های بسته بندی، ورق های ترموفرمینگ و قالبگیری تزریقی مورد استفاده می شود[۸].
روش های تولید پلی پروپیلن
تولید پلی پروپیلن به دو روش دوغابی و گازی امکان پذیر است. در روش دوغابی از حلال هایی چون بوتان، هپتان و حتی پارافین های سنگین تر به عنوان حلال استفاده می شود. وظیفه حلال علاوه بر مهیا سازی بستر پلیمریزاسیون، محصول جانبی ( پلی پروپیلن اتاکتیک) را از محیط حذف می کند. استفاده از این روش نیازمند فضای بزرگ، ابزار و دستگاههای متعدد و … می باشد لذا هزینه های اولیه و ثانویه بالایی دارد. به همین دلیل استفاده از سیستم ها بالک دوغابی پیشنهاد شد که مایع پروپیلن به عنوان جایگزین حلال در محیط وارد می شود. در این روش بر خلاف روش قبل که کاتالیست های نوع اول و دوم مورد استفاده قرار می گرفت، بهره گیری از کاتالیست های نوع سوم نیز امکان پذیر شد.
روش گازی به منظور حذف فاز مایع و همچنین مراحل جداسازی حلال معرفی شد. در این روش مونومر به همراه کاتالیست و افزودنی ها اضافه شده و پس از انجام فرآیند پلیمریزاسیون، کاتالیست از محیط حذف می شود. طرح شماتیک فرآیندهای بالک دوغابی و گازی در شکل های ۱۴ و ۱۵ آمده است[۸].
به طور کلی پلی الفین ها به عنوان پر مصرف ترین پلاستیک ها در دنیا شناخته می شوند. این دسته از پلیمر ها در خواصی نظیر مدول خمشی، مقاومت کششی و سختی سطح، نسبت به پلیمر های هم قیمت خود برتری دارند. جدول ۶ به طور خلاصه مقایسه ای بین پلی الفین ها با PVC, ABS و HIPS ارائه می دهد.
جدول ۶٫ مقایسه پلی الفین ها با برخی پلیمر ها
هرچه فشار راکتور بالاتر باشد، جرم مولکولی پلی اتیلن نهایی بیشتر خواهد بود، از طرفی با افزایش دمای پلیمریزاسیون، امکان حرکت زنجیر ها راندوم بیشتر و درصد شاخه های جانبی افزایش می یابد. آغازگر مورد استفاده نیز بر مبنای دمای عملکردی و از شرایط واکنش تعیین می شود، بنابراین استفاده از آغازگرهای پروکسیدی به دلیل دمای عملکردی پایین باعث کاهش شاخه ای شدن خواهد شد.
پلی اتیلن سنگین HDPE و پلی اتیلن سبک خطی LLDPE
استفاده از کاتالیست های زیگلر- ناتا و متالوسن، امکان تولید زنجیر های پلی اتیلنی با درصد شاخه پایین را فراهم کرد. بر خلاف پلیمریزاسیون پلی اتیلن سبک، واکنش پلیمریزاسیون در حضور کاتالیست های زیگلر- ناتا و متالوسنی در دما و فشار پایین انجام می شود. همچنین علاوه بر اتیلن، برخی دیگر از آلکان ها نیز در حضور کاتالیست های زیگلر- ناتا پلیمریزه می شوند، بنابراین تولید هموپلیمر و کوپلیمر های آلکانی با استفاده از این کاتالیست ها امکان پذیر می باشد. از این رو دستیابی به پلی اتیلن سنگین و پلی اتیلن سبک خطی امکان پذیر شد.
شکل ۸٫ طرح شماتیک راکتور فشار پایین ( محلولی )
شکل ۱۲٫ ساختار پلی پروپیلن
شکل ۱۵٫ فرآیند گازی
References
WWW.Wikipedia.com
Plastics Europe ” Association of Plastic Manufacturers”
Andrew Peacock “Handbook of Polyethylene ” Marcel Dekker Inc.
M.C. Sobieraj, C.M. Rimnac ” Ultra high molecular weight polyethylene: Mechanics, morphology, and clinical behavior ” Journal of Mechanical Behavior of Biomedical Materials 2, 433-443
Denis B. Malpass ” Introduction to Industrial Polyethylene ” Wiley 2010
Cornelia Vasile, Michaela Pascu ” Practical Guide to Polyethylene ” Rapra Technology Limited
Devesh Tripathi ” Practical Guide to Polypropylene ” Rapra Technology Limited
Harutun G. Karian ” Handbook of Polypropylene and Polypropylene Composites” Rhetech
درصد و اندازه شاخه های جانبی بر روی میزان بلورینگی زنجیر ها تاثیر می گذارد. به این ترتیب با افزایش درصد و اندازه شاخه ها، بلورینگی کاهش می یابد و در نتیجه چگالی پلیمر نهایی کمتر خواهد بود[۳]. پر مصرف ترین پلی اتیلن ها LDPE,LLDPE و HDPE می باشند ولی در این بین گرید هایی نظیر UHMWPE و MDPE نیز در مصارف خاص مورد استفاده قرار می گیرند.
LDPE
درصد بالای شاخه های جانبی با اندازه های بزرگ و کوچک، مانع از ایجاد کریستال می شود در نتیجه چگالی پلیمر نهایی در بازه g/cm۳ 94/۰ – ۹۱/۰ ، ویسکوزیته پایین، مقاومت مذاب بالا و فرآیند پذیری مناسب خواهد بود. از این رو عمده مصرف پلی اتیلن سبک در تولید فیلم های دمشی می باشد.
شکل ۲٫ ساختار پلی اتیلن سبک (LDPE )
جدول ۱٫ گرید های مختلف پلی اتیلن سبک
شکل ۳٫ ساختار پلی اتیلن سنگین (HDPE )
پلی اتیلن سبک خطی (LLDPE) و پلی اتیلن بسیار سبک ( VLDPE)، طیف وسیعی از پلی اتیلن ها، از شفاف و الاستومری تا کدر و سفت و خشک را شامل می شود. با توجه به ساختار زنجیر، این پلیمر خواصی مشابه با پلی اتیلن سبک و پلی اتیلن سنگین نشان می دهد، از این رو در مواردی که سفتی و مقاومت بالا در کنار چگالی پایین و انعطاف پذیری بالا مد نظر باشد مورد استفاده قرار می گیرد. ظروف بسته بندی مواد غذایی، تانک های ذخیره سازی و روکش کابل ها از این دسته از پلیمر ها تهیه می شوند. از طرفی با افزایش درصد کومونومر، چگالی پلیمر کاهش می یابد و پلی اتیلن بسیار سبک با خواصی نظیر شفافیت، چقرمگی و نرمی به دست می آید که در تولید لوله های پزشکی و بسته بندی گوشت استفاده دارد.
شکل ۴٫ ساختار پلی اتیلن سبک خطی ( LLDPE )
شکل ۶٫ رابطه MFI پلی اتیلن سبک خطی با جرم مولکولی
به منظور تولید پلی اتیلن با ساختار کنترل شده علاوه بر استفاده از کاتالیست، طراحی راکتور نیز باید تغییر بکند (شکل ۸). اتیلن خالص پس از فشرده شدن در کمپرسور شماره ۱، وارد راکتور ۲ شده و با کاتالیست، کو کاتالیست و حلال ورودی از تانکرهای ۴،۳ و ۵ ترکیب و پلیمریزاسیون را شروع می کند. حرارت ایجاد شده در اثر واکنش با استفاده از دستگاه های خنک کننده خارج شده و حلال تبخیر شده نیز وارد کمپرسور ۶ شده و پس از میعان به راکتور باز می گردد. پس از اتمام پلیمریزاسیون مخلوط g شامل پلی اتیلن، حلال و کاتالیست وارد جدا کننده ۷ شده، حلال آن بازیافت شده و مجددا به ورودی باز گردانده می شود، کاتالیست باقی مانده نیز با استفاده از حلال مخصوص جدا شده و پلیمر خالص بدست می آید.
استفاده از کومونومر های الفینی نظیر ۱-بوتن ،۱-هگزن و ۱- اکتن دستیابی به پلی اتیلن سبک خطی را امکان پذیر می سازد. همچنین استفاده از درصد بالا از پروپن باعث دستیابی به لاستیک EPDM می شود. افزایش درصد کومونومر باعث باعث کاهش بلورینگی و در نتیجه کاهش چگالی و افزایش نرمی و انعطاف پذیری پلیمر نهایی می شود[۳].
شکل ۹٫ گرید های مختلف پلی اتیلن {۶}
پلی پروپیلن
دومین پلاستیک پر مصرف در دنیا، که ۲۳ درصد کل تولید پلاستیک جهان را در سال ۲۰۱۵ شامل می شده است، پلی پروپیلن نام دارد[۲]. این دسته از مواد از خانواده پلی الفین ها بوده و تفاوت ساختار آنها با پلی اتیلن خالص در شاخه های تکرار شونده آن می باشد. در شکل ۱۰ ساده ترین ساختار پلی پروپیلن نشان داده شده است.
شکل ۱۰٫ ساختار پلی پروپیلن خالص ( ساده ترین ساختار )
سنتز این پلیمر نخستین بار توسط زیگلر و ناتا انجام در سال ۱۹۵۴ انجام گرفت. زنجیر پلی پروپیلن در هر واحد تکراری دارای استخلاف متیل بوده که جهت گیری فضایی آنها باعث به وجود آمدن انواع مختلف پلی پروپیلن می شود. پر مصرف ترین گرید پلی پروپیلن Isotactic بوده که تمامی استخلاف های متیل در یک سمت قرار می گیرند. با توجه به نظم بالای زنجیر در این گرید پلی پروپیلن، درصد بلورینگی بالایی در آن مشاهده می شود. در صورتی که استخلاف های متیل به صورت یک در میان در بالا و پایین زنجیر قرار گیرند، گرید Syndiotactic بوجود می آید که قابلیت بلورینگی آن کمتر از گرید Isotactic بوده و خواصی ضعیف تر از آن ارائه می دهد. ضعیف ترین خواص را پلی پروپیلن Atactic دارد که استخلاف های آن به صورت نامنظم در بالا و پایین زنجیر قرار می گیرد. ساختار گرید های پلی پروپیلن در شکل های ۱۳-۱۱ ارائه شده است[۳].
شکل ۱۱٫ ساختار پلی پروپیلن
شکل ۱۳٫ ساختار پلی پروپیلن
به منظور بهبود خواص پلی پروپیلن، به جای هموپلیمر، از کوپلیمر های رندوم و قطعه ای با بهره گیری از کومونومر اتیلن و یا دیگر آلکنها ( نظیر ۱-بوتن) ، استفاده می شود. کوپلیمر رندوم، درصد کریستال کمتری دارد در نتیجه مقاومت به ضربه بالاتر، بازه دمایی پهن تر و شفافیت بالاتر خواهد داشت. از طرفی کوپلیمر قطعه ای با داشتن دو فاز متفاومت رابری و کریستالی ناشی از زنجیر های کوپلیمر و زنجیرهای زنجیر های هموپلیمر، چقرمگی بالاتر، شفافیت بیشتر و مقاومت به ضربه بالاتری خواهد داشت[۷].
جدول ۵٫ گریدهای مختلف هموپلیمر پلی پروپیلن
مقالات مرتبط :
سلام
یه نکته این که هر پلی الفین از یه الفین خاص تهیه شده که از اسم اون پلی الفین میشه تشخیص داد.
سلام
با تشکر از محتوای خوبتون. پلیمری که از ۲ نوع یا بیشتر مونومر ساخته شده است، کوپلیمر نام دارد و کوپلیمر طی فرآیندی که به آن کوپلیمریزاسیون میگویند، تشکیل می شود.
سلام
پلی الفین چه فرقی با سایر پلیمرها دارد؟
سلام
پلی الفین در ویژگی هایی از جمله مدول خمشی، مقاومت کششی و سختی سطح نسبت به سایر پلیمرها برتری دارد.
سلام
میخواستم بدونم نقطه ذوب پلی افیلن ها حدودا چقدر هست؟
پلی افیلن ها معمولا در دمای ۱۳۰ تا ۱۶۰ درجه سانتی گراد حل می شوند اما نکته ای که مطرح است این است که پلی افیلن ها در حلال هایی با نقطه جوش بالا مانند دی کلروبنزن، تری کلروبنزن یا دکاهیدرونفتالین قرار می گیرند و این نقطه جوش را دارند.