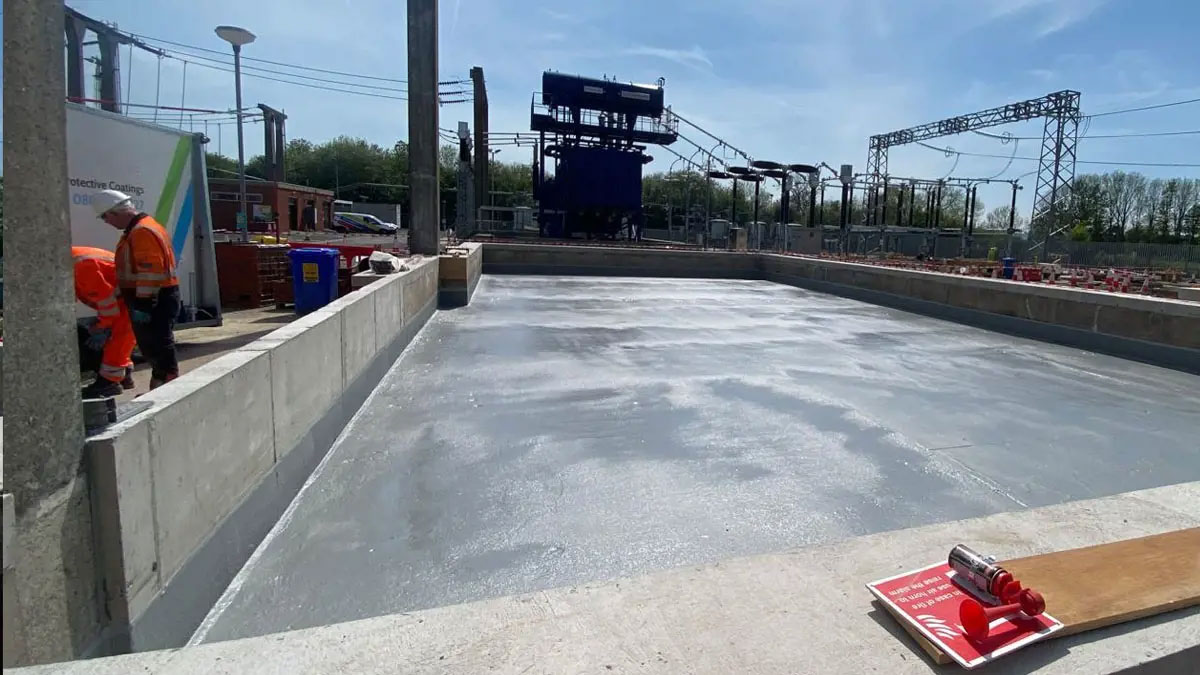
Bund lining is an essential practice in industries that handle hazardous substances, ensuring that leaks and spills are contained effectively to protect both the environment and infrastructure. In this article we discuss about its benefits, types and process.
What does bund lining mean?
Bund lining refers to the protective layer applied to bunds (secondary containment structures) to prevent leaks or seepage of hazardous liquids, such as chemicals, oils, or fuels. Bunds are designed to contain spills from storage tanks, pipelines, or industrial facilities, and lining them ensures that the contained substances do not seep into the ground, protecting the environment.
Bund linings can be made of different materials, including:
- Concrete coatings (epoxy, polyurethane)
- Geomembranes (HDPE, PVC)
- Rubber or polymer linings
- Clay-based linings
The choice of material depends on the type of liquid being contained, environmental regulations, and site-specific conditions.
What are the benefits of bund lining?
Bund lining offers several key benefits that enhance the effectiveness and durability of containment systems:
- Environmental Protection: By creating an impermeable barrier, bund linings prevent hazardous substances from seeping into the ground, thereby protecting soil and groundwater from contamination.
- Structural Integrity: High-quality linings, such as fibreglass and polyurea, provide robust structural support to bunds, extending their lifespan and ensuring they remain effective over time.
- Chemical Resistance: Properly selected linings resist chemical attacks, safeguarding the underlying bund structure from degradation caused by stored substances.
- Regulatory Compliance: Implementing effective bund linings helps industries adhere to environmental regulations, avoiding potential fines and demonstrating a commitment to environmental responsibility.
- Cost Efficiency: By preventing leaks and structural damage, bund linings reduce the need for costly repairs and environmental remediation efforts, leading to long-term financial savings.
Different types of bund linings
Bund linings come in various types, each designed for specific containment needs based on the chemicals being stored, environmental conditions, and durability requirements. Here is some common bund lining types:
1. Concrete-Based Linings
- Epoxy Coatings – Provide a seamless, chemical-resistant surface, ideal for industrial applications.
- Polyurethane Coatings – Flexible and impact-resistant, suitable for high-traffic areas.
2. Geomembrane Linings
- HDPE (High-Density Polyethylene) – Highly resistant to chemicals, UV exposure, and punctures.
- PVC (Polyvinyl Chloride) – Flexible and cost-effective but less resistant to harsh chemicals than HDPE.
- LDPE (Low-Density Polyethylene) – Offers more flexibility than HDPE but is less durable.
3. Rubber & Polymeric Linings
- Butyl Rubber Linings – Excellent resistance to oils, fuels, and chemicals.
- Polyurea Linings – Fast-curing, highly durable, and suitable for high-impact applications.
4. Fiberglass Reinforced Linings (FRP)
- Strong, lightweight, and highly resistant to corrosion, commonly used in chemical plants.
5. Clay-Based Linings
- Bentonite Liners – Naturally swelling clay that provides an impermeable barrier, often used in environmental containment.
The role of geosynthetics in bund lining
Geosynthetic products play a crucial role in bund lining, providing cost-effective, durable, and efficient solutions for containment structures. These materials, which include geomembranes, geotextiles, geogrids, and geocells, are engineered to perform specific functions that enhance the effectiveness of bunds. Here’s how they contribute:
1. Impermeability and Leak Prevention
- Geomembranes, such as HDPE and PVC, offer a seamless, impermeable layer that prevents the seepage of hazardous liquids like oils, chemicals, and fuels into the ground. This is vital for protecting soil and groundwater from contamination.
2. Strength and Durability
- Geosynthetics like geogrids reinforce bund structures, providing additional strength to withstand the pressure of contained liquids and external forces (e.g., traffic or heavy machinery).
- Fiberglass or polymer-based linings offer enhanced durability, especially in aggressive chemical environments, reducing the risk of structural failure.
3. Cost-Effectiveness
- Geosynthetics are typically more affordable compared to traditional bund lining materials (e.g., concrete). They offer a more efficient solution, especially for large-scale containment projects, by reducing labor and installation time.
4. Environmental Protection
- Geosynthetics are designed to provide long-term protection. Geomembranes, in particular, act as a reliable barrier to hazardous substances, preventing contamination of surrounding ecosystems and complying with environmental regulations.
5. Ease of Installation and Maintenance
- The lightweight nature of geosynthetics makes them easier to handle and install, minimizing disruption on-site.
- Additionally, many geosynthetic materials are resistant to UV degradation, weathering, and wear, reducing the frequency of maintenance or replacement.
6. Flexibility and Adaptability
- Geosynthetic materials are highly flexible and can be adapted to a wide range of soil conditions and bund shapes. This makes them ideal for both new bunds and retrofitting existing structures.
7. Enhanced Safety
- By providing a reliable containment barrier, geosynthetics help minimize the risk of spills and environmental damage, ensuring compliance with health, safety, and environmental standards.
Bund lining process: Stages needed
The bund lining process involves several stages to ensure that the bund is effectively sealed and protected from potential leaks or seepage. Here’s an outline of the typical stages involved in the process:
1. Site Preparation
- Clearing and Grading: The bund area is cleared of debris, vegetation, and any other obstacles. The ground is graded to ensure proper drainage and uniform thickness for the lining material.
- Soil Testing: In some cases, soil tests are conducted to determine the compatibility of the soil with the lining material, and to assess whether additional groundwork is needed.
2. Excavation
- The bund structure is excavated to the required shape and dimensions, ensuring it can contain the desired volume of liquid.
- The base and sides are prepared to ensure that the foundation is stable and suitable for lining installation.
3. Subgrade Preparation
- The base of the bund is compacted to a firm and stable level. This helps in providing a solid foundation for the liner and preventing future subsidence.
- Geotextile fabric may be laid down over the subgrade to protect the liner from punctures caused by sharp objects in the soil.
4. Installation of Lining Material
- Geomembranes (e.g., HDPE, PVC) or other chosen materials like polyurea, polyurethane, or rubber linings are installed, depending on the specific requirements (chemical resistance, flexibility, etc.).
- The lining is carefully laid out, ensuring there are no folds or wrinkles. It is usually welded or sealed at the seams to create a continuous, impermeable surface.
- Overlap and Sealing: Overlapping seams are welded or sealed with heat, adhesives, or mechanical fasteners, ensuring they are watertight.
5. Quality Control and Testing
- During installation, regular visual inspections are conducted to check for any defects or potential installation issues.
- Leak detection or pressure testing may be performed to ensure that the lining is fully sealed and impermeable. Air or water testing can identify any leaks or weak spots in the system.
6. Backfilling and Covering
- After the lining is in place and the seams are sealed, the bund is backfilled with suitable material to protect the lining. In some cases, a protective layer of geotextile fabric or gravel may be added over the liner.
- Care is taken during backfilling to prevent any damage to the liner from sharp materials.
7. Final Inspection and Compliance Check
- A final inspection is performed to ensure that the bund is fully compliant with environmental regulations and industry standards.
- The bund is assessed for any remaining potential weaknesses and to confirm that it meets the required capacity.
8. Maintenance and Monitoring
- Once installed, the bund should be regularly monitored and maintained. This involves checking the integrity of the lining, performing repairs as necessary, and ensuring no leaks or environmental hazards arise.
- Maintenance schedules are often outlined in accordance with regulatory requirements, ensuring the bund continues to provide effective containment throughout its lifespan.
Conclusion
In conclusion, bund lining is a critical process for ensuring the safe and effective containment of hazardous substances, protecting both the environment and the surrounding infrastructure. Its primary benefits include preventing leakage, enhancing structural integrity, offering chemical resistance, and ensuring compliance with environmental regulations.