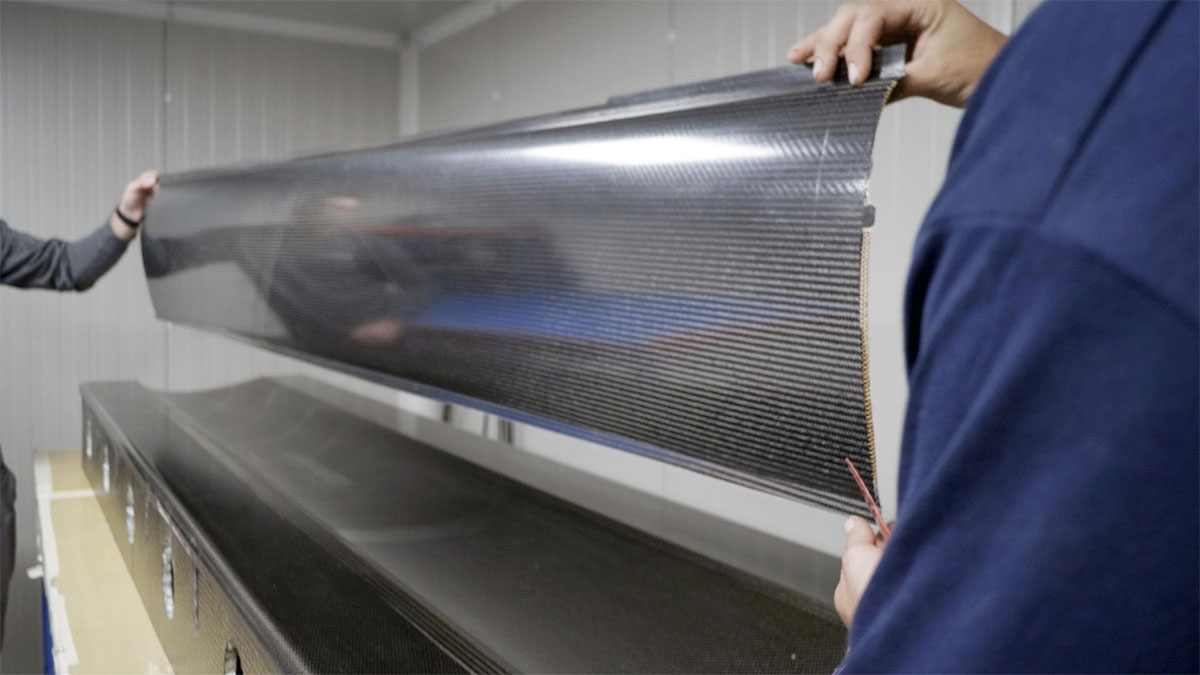
Composite materials have emerged as game-changers in various industries, offering a remarkable combination of lightweight construction, exceptional strength, and tailored properties, revolutionizing the way we design and build. We want to talk about composite materials advantages.
What are composite materials?
Composite materials are materials made up of two or more distinct constituent materials that, when combined, create a new material with enhanced properties. These constituent materials can have different physical and chemical properties, such as strength, stiffness, density, thermal conductivity, and electrical conductivity.
The purpose of combining different materials in a composite is to take advantage of the desirable properties of each constituent while minimizing their individual limitations. By carefully selecting and arranging the components, composites can be engineered to exhibit specific characteristics that are not achievable with any single material alone.
Read more: What are geocomposite materials?
Composite materials advantages
Composite materials offer several advantages over traditional materials, which contribute to their widespread use in various industries. Here are some key benefits of composite materials:
- High Strength-to-Weight Ratio: Composites are known for their exceptional strength-to-weight ratio. They possess high strength and stiffness while being significantly lighter than traditional materials like metals. This property is particularly important in industries such as aerospace and automotive, where weight reduction is critical for fuel efficiency and performance.
- Tailorable Properties: Composite materials can be engineered to possess specific properties by selecting appropriate reinforcements and matrix materials. By adjusting the composition, orientation, and volume fraction of the reinforcement, composites can be customized to meet specific performance requirements such as strength, stiffness, thermal conductivity, and electrical conductivity.
- Design Flexibility: Composites offer designers greater freedom in creating complex shapes and structures. They can be molded into various forms, allowing for intricate geometries and streamlined designs. This flexibility enables optimization of structures for enhanced performance and functionality.
- Corrosion Resistance: Unlike metals, many composite materials are inherently resistant to corrosion, making them suitable for applications in harsh environments. This property eliminates the need for additional protective coatings or treatments, reducing maintenance and extending the lifespan of the components.
- Fatigue Resistance: Composites exhibit excellent fatigue resistance, meaning they can withstand repeated loading and unloading cycles without significant degradation in performance. This property is beneficial in applications subjected to cyclic loading, such as aircraft wings, wind turbine blades, and sporting equipment.
- Thermal and Electrical Insulation: Depending on the composition, composites can provide excellent thermal and electrical insulation properties. This makes them suitable for applications where insulation is required, such as electronic enclosures, aerospace heat shields, and thermal barriers in buildings.
- Impact Resistance: Composites can effectively absorb and distribute energy upon impact, making them highly resistant to damage from impacts and collisions. This property is vital in applications where impact resistance is crucial, such as body armor, sports helmets, and automotive crash structures.
- Chemical Resistance: Certain composite materials exhibit excellent resistance to chemicals, acids, and corrosive substances. This property allows them to be used in environments where exposure to chemicals is common, such as chemical processing plants, storage tanks, and marine applications.
- Acoustic Damping: Composites can be engineered to possess sound-damping properties, reducing noise and vibration levels. These materials find applications in aerospace, automotive, and architectural industries, where noise control is essential.
>> Geocomposite sheets price in Farnam Baspar company
The applications of composite materials in various industries
Composite materials find extensive applications in numerous industries due to their unique properties and advantages. Here are some examples of how composite materials are used in various industries:
- Aerospace: Composite materials play a crucial role in aerospace applications. They are used in aircraft structures, including wings, fuselages, empennages, and interior components. Composites offer significant weight reduction, fuel efficiency, and improved performance, making them ideal for aerospace applications. Carbon fiber-reinforced polymers (CFRP) are commonly used in aerospace due to their high strength-to-weight ratio.
- Automotive: Composites are used in the automotive industry for lightweighting vehicles, reducing fuel consumption, and improving efficiency. Carbon fiber composites and glass fiber composites are employed in parts such as body panels, chassis components, interior parts, and engine components. Composites offer enhanced strength, crash resistance, and design flexibility in automotive applications.
- Construction: Composites are utilized in the construction industry for various purposes. They are used in building structures, bridges, and infrastructure elements such as rebar, beams, columns, and facades. Composite materials offer high strength, corrosion resistance, durability, and design versatility, allowing for innovative architectural designs and sustainable construction practices.
- Marine: Composite materials are extensively used in the marine industry due to their corrosion resistance, high strength, and lightweight properties. They find applications in boat hulls, decks, masts, and other structural components. Fiberglass composites are commonly employed in marine applications due to their excellent water resistance and durability.
- Sports and Recreation: Composite materials have revolutionized the sports and recreation industry by providing high-performance equipment. Carbon fiber composites are widely used in sporting goods such as tennis rackets, golf clubs, bicycle frames, hockey sticks, and skis. These materials offer superior strength, stiffness, and impact resistance, enhancing athletes’ performance.
- Renewable Energy: Composite materials are utilized in renewable energy applications such as wind turbines and solar panels. Wind turbine blades often incorporate composites due to their strength, durability, and fatigue resistance. Composites are also used in the construction of rotor blades for tidal and wave energy devices.
- Electronics and Electrical: Composite materials find application in the electronics and electrical industry. They are used in circuit boards, electrical insulators, and enclosures due to their excellent electrical insulation properties. Composites offer thermal insulation, chemical resistance, and protection against electromagnetic interference.
- Medical and Healthcare: Composite materials have made advancements in medical and healthcare applications. They are used in prosthetics, orthopedic implants, dental materials, and medical equipment. Composites provide biocompatibility, lightweight design, and the ability to mimic natural properties, improving patient comfort and outcomes.
- Defense and Military: Composite materials are employed in defense and military applications, including armored vehicles, ballistic protection, aircraft components, and radomes. Composites offer high strength, impact resistance, and reduced weight, enhancing the performance, mobility, and protection of military assets.
Composite materials VS traditional materials
Composite materials and traditional materials have distinct differences in their properties and characteristics. Here is a comparison between composite materials and traditional materials:
- Composition: Traditional materials are typically homogeneous substances, such as metals (e.g., steel, aluminum), ceramics, woods, and plastics. Composite materials, on the other hand, are heterogeneous materials composed of two or more distinct components, such as a matrix material and reinforcement materials (e.g., fibers, particles).
- Weight: Composite materials offer a significant advantage in terms of weight reduction compared to traditional materials. Composites can be engineered to be lightweight while maintaining high strength, resulting in improved fuel efficiency, performance, and ease of handling.
- Strength-to-Weight Ratio: Composite materials have a higher strength-to-weight ratio than traditional materials. This means they can exhibit comparable or superior strength and stiffness while being significantly lighter. Traditional materials often have lower strength-to-weight ratios, making them heavier for the same level of strength.
- Design Flexibility: Composites offer greater design flexibility compared to traditional materials. They can be molded into complex shapes and structures, allowing for innovative designs with optimized performance. Traditional materials may have limitations in terms of shaping and forming, restricting design possibilities.
- Specific Properties: Composite materials can be tailored to exhibit specific properties by selecting appropriate reinforcement materials and adjusting their volume fractions. This allows for customization of properties such as strength, stiffness, thermal conductivity, electrical conductivity, and corrosion resistance. Traditional materials have inherent properties that may be more difficult to modify or enhance.
- Corrosion Resistance: Composites, particularly those with polymer matrix materials, often exhibit excellent corrosion resistance compared to traditional metals. This property reduces the need for additional protective coatings or treatments, leading to lower maintenance requirements and longer component lifespans.
- Cost: The cost of composite materials can vary depending on factors such as the type of reinforcement, matrix material, and manufacturing processes involved. In general, composites tend to be more expensive than traditional materials. However, advancements in manufacturing technologies and increased adoption have led to cost reductions in some composite applications.
- Manufacturing Processes: Traditional materials often have well-established and mature manufacturing processes, making them readily available and easier to produce in large quantities. Composite materials may require more specialized manufacturing techniques, such as layup, resin infusion, or filament winding, which can be more complex and time-consuming.
- Repair and Maintenance: Repairing and maintaining composite materials can be more challenging compared to traditional materials. Damaged composites often require specialized repair techniques and expertise to restore their original properties. Traditional materials may have simpler repair and maintenance procedures.
>> Geosynthetic products price in Farnam Baspar company
Future trends in composite technology
Composite technology is rapidly evolving, driven by advancements in materials science, manufacturing processes, and a growing demand for high-performance materials across various industries. Here are some future trends in composite technology:
1. Advanced Materials Development
- Nanocomposites: Integration of nanomaterials such as carbon nanotubes, graphene, and nanoclays to enhance mechanical, thermal, and electrical properties.
- Bio-based Composites: Increased use of sustainable, biodegradable, and bio-based materials to reduce environmental impact.
- Smart Composites: Development of composites with embedded sensors and actuators for real-time monitoring and adaptive functionalities.
2. Manufacturing Innovations
- Additive Manufacturing (3D Printing): Use of 3D printing for creating complex composite structures with tailored properties and reduced material waste.
- Automated Fiber Placement (AFP): Enhanced automation techniques for precise placement of fibers, improving production efficiency and consistency.
- Out-of-Autoclave (OoA) Processes: Development of manufacturing methods that do not require autoclaves, such as resin transfer molding (RTM) and vacuum-assisted resin infusion (VARI), to lower costs and energy usage.
3. Improved Performance and Durability
- High-Temperature Composites: Research into materials that can withstand extreme temperatures for applications in aerospace, automotive, and energy sectors.
- Multi-Functional Composites: Composites that offer additional functionalities such as self-healing, electrical conductivity, and impact resistance.
- Lightweighting: Continuous efforts to reduce weight while maintaining or enhancing strength, particularly important for transportation and aerospace industries.
4. Sustainability and Recycling
- Recyclable Composites: Development of composites that can be more easily recycled or repurposed at the end of their life cycle.
- Eco-Friendly Production Methods: Adoption of greener production techniques to reduce environmental impact and carbon footprint.
5. Industry-Specific Applications
- Aerospace: Use of advanced composites for next-generation aircraft, UAVs, and space vehicles to improve fuel efficiency and performance.
- Automotive: Increased application of composites in electric vehicles (EVs) for weight reduction and enhanced battery performance.
- Construction: Composites in infrastructure for durable, corrosion-resistant, and lightweight building materials.
6. Digitalization and Simulation
- Digital Twins: Implementation of digital twin technology for real-time monitoring, predictive maintenance, and lifecycle management of composite structures.
- Simulation and Modeling: Advanced computational tools for the design and testing of composites, reducing the need for physical prototypes and accelerating development cycles.
7. Regulations and Standards
- Standardization: Development of industry-wide standards and regulations to ensure safety, reliability, and interoperability of composite materials and products.
8. Collaboration and Innovation
- Cross-Disciplinary Research: Collaboration between academia, industry, and government agencies to drive innovation and address technical challenges.
- Open Innovation Platforms: Use of open innovation platforms and consortia to share knowledge, resources, and accelerate advancements in composite technology.
Conclusion
Composite materials offer several advantages over traditional materials. They possess a high strength-to-weight ratio, allowing for lightweight structures without compromising strength and durability. We have many types of composite materials and they can be tailored to exhibit specific properties, such as strength, stiffness, and corrosion resistance, providing flexibility in design and meeting application requirements.