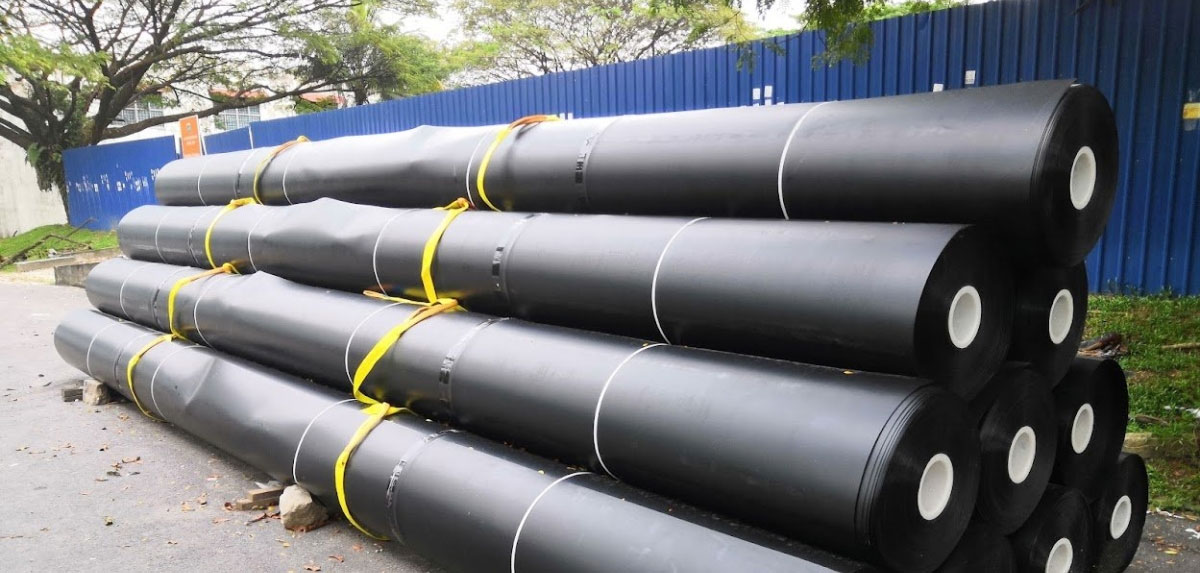
Choosing the right geomembrane is crucial for project success, considering factors like application, site conditions, material properties, installation/maintenance needs, regulations, manufacturer reputation, and cost-effectiveness. In this post we discuss about geomembrane selection factors.
What is a geomembrane
A geomembrane sheet is a synthetic material used in geotechnical engineering and environmental applications. It is a thin, flexible sheet made from various polymer materials, such as high-density polyethylene (HDPE), low-density polyethylene (LDPE), polyvinyl chloride (PVC), or ethylene propylene diene monomer (EPDM).
Geomembranes are designed to provide a barrier against fluids, gases, and contaminants in a wide range of applications. They are commonly used for containment purposes, such as lining landfills, ponds, reservoirs, and canals to prevent leakage or seepage. Geomembranes can also be used in environmental protection projects, such as secondary containment for chemical storage, wastewater treatment ponds, or mining operations.
Geomembrane material type
Geomembranes are available in various material types, each with its own properties and suitability for different applications. Here are some commonly used geomembrane material types:
- High-Density Polyethylene (HDPE): HDPE geomembranes are widely used due to their excellent chemical resistance, high tensile strength, and durability.
- Low-Density Polyethylene (LDPE): LDPE geomembranes offer good flexibility and elongation properties.
- Polyvinyl Chloride (PVC): PVC geomembranes provide good chemical resistance and are commonly used in applications involving industrial wastewater, chemical storage, and landfill liners.
- Ethylene Propylene Diene Monomer (EPDM): EPDM geomembranes are known for their excellent weathering resistance and flexibility over a wide temperature range.
- Polypropylene (PP): PP geomembranes offer high chemical resistance and are often used in applications involving aggressive chemical environments, including chemical storage facilities, wastewater treatment plants, and industrial containment.
- Chlorosulfonated Polyethylene (CSPE): CSPE geomembranes, also known as Hypalon, exhibit excellent resistance to ozone, UV radiation, and a wide range of chemicals.
Geomembrane thickness
Here are some common ranges of geomembrane thickness for different applications:
- Landfill Liners: Geomembranes used as liners in landfills typically range from 0.75 mm (30 mil) to 2.0 mm (80 mil) in thickness. The specific thickness depends on factors such as waste type, liner design, and regulatory requirements.
- Pond Liners: Geomembranes used as liners for ponds, reservoirs, or water containment structures can vary in thickness. Generally, they range from 0.5 mm (20 mil) to 1.5 mm (60 mil) based on the size of the pond, water depth, and environmental conditions.
- Secondary Containment: Geomembranes used for secondary containment systems, such as chemical storage areas or industrial spill containment, typically range from 0.75 mm (30 mil) to 1.5 mm (60 mil) in thickness. Thicker geomembranes may be required for applications involving more aggressive chemicals.
- Mining Applications: Geomembranes used in mining applications, such as heap leach pads or tailings ponds, can vary in thickness depending on the specific requirements and site conditions. They commonly range from 0.75 mm (30 mil) to 2.0 mm (80 mil) or even thicker for certain applications.
Understanding the geomembrane environment
Here are key aspects to consider when seeking to understand the geomembrane environment:
- Site Conditions: Evaluate the physical properties of the site, such as soil type, slope, groundwater levels, and climate.
- Chemical Compatibility: Assess the chemical composition and potential exposure of the geomembrane to substances present in the environment or in contact with the geomembrane. Consider the pH levels, concentrations, and types of chemicals or contaminants to select a geomembrane material that is chemically compatible and resistant.
- Temperature and UV Exposure: Analyze the temperature range and variations that the geomembrane will experience, as well as the level of ultraviolet (UV) radiation exposure. Different geomembrane materials have varying resistance to temperature extremes and UV degradation, and understanding these factors helps choose a suitable geomembrane for the environment.
- Installation and Construction Processes: Understand the installation methods, techniques, and quality control measures specific to geomembranes. Factors such as seam integrity, anchoring systems, tensioning, and protection layers can significantly impact the performance and longevity of geomembranes.
- Risk Assessment: Identify potential risks or challenges that may affect the geomembrane system, such as subsurface conditions, seismic activity, nearby structures, or external forces. Evaluating these risks helps design and implement mitigation measures to enhance the geomembrane’s integrity and performance.
- Regulatory Compliance: Consider the applicable regulations, standards, and guidelines related to geomembrane installations in the specific environment. Compliance with these requirements ensures that the geomembrane system meets the necessary performance and environmental protection criteria.
Geomembrane durability
Several factors influence the durability of geomembranes:
- Material Selection: The choice of geomembrane material plays a significant role in determining its durability. Different materials, such as high-density polyethylene (HDPE), polyvinyl chloride (PVC), or ethylene propylene diene monomer (EPDM), have varying resistance to UV degradation, chemical attack, puncture, and aging. Selecting a material with suitable properties for the intended application is crucial for long-term durability.
- UV Resistance: Exposure to ultraviolet (UV) radiation from sunlight can degrade geomembranes over time. UV stabilizers are often incorporated into geomembrane formulations to enhance their resistance to UV degradation. The thickness and composition of the geomembrane, as well as the presence of protective layers or coatings, can also influence its UV resistance and overall durability.
- Chemical Resistance: Geomembranes may come into contact with various chemicals or contaminants in their applications. Assessing the chemical compatibility of the geomembrane material with the specific substances it will encounter is essential. Some geomembrane materials exhibit excellent resistance to a wide range of chemicals, while others may require additional protective measures or specialized formulations for enhanced durability in chemically aggressive environments.
- Mechanical Strength: Geomembranes should possess sufficient mechanical strength to withstand installation stresses, including handling, anchoring, and tensioning. They should also resist puncture, tearing, and abrasion caused by sharp objects or moving loads. The thickness and reinforcement options, such as geotextiles or geogrids, can be considered to enhance the mechanical strength and durability of geomembranes.
- Environmental Conditions: The specific environmental conditions, including temperature extremes, moisture levels, freeze-thaw cycles, and soil or water chemistry, can impact geomembrane durability. Understanding the anticipated environmental conditions and selecting a geomembrane material with appropriate properties and resistance to these conditions is vital for long-term performance.
- Quality Control and Installation: Proper installation techniques, including seam integrity, welding or joining methods, and quality control measures, are critical for ensuring the long-term durability of geomembranes. Inadequate installation practices can compromise the integrity of the geomembrane system and lead to premature failure.
Geomembrane site conditions
Here are key site conditions to consider:
- Soil Type and Properties: The soil type and its properties, such as permeability, compaction, and shear strength, affect the performance of geomembranes. Different soils require different approaches to ensure proper anchorage and prevent potential issues like punctures or slippage.
- Slope Stability: If the site has slopes or embankments, slope stability analysis is necessary. Understanding the stability of the slopes helps in designing reinforcement measures, such as geogrids or geotextiles, to prevent erosion or movement that may compromise the geomembrane’s integrity.
- Groundwater Level and Flow: The presence and behavior of groundwater are critical considerations. High groundwater levels or fluctuating water tables can exert hydrostatic pressure on the geomembrane. Assessing groundwater flow patterns and potential seepage paths helps in designing drainage systems and appropriate liner configurations.
- Climate and Weather Conditions: Climate factors including temperature range, precipitation levels, wind speeds, and freeze-thaw cycles influence geomembrane performance. Extreme temperatures, for instance, can affect the material properties and flexibility of geomembranes. Understanding climatic conditions aids in selecting geomembrane materials with suitable temperature and weather resistance.
- Chemical Exposure: If the site involves the storage or containment of hazardous or aggressive chemicals, assessing the potential chemical exposure is crucial. Analyzing the chemical composition, concentration, and pH levels of the substances helps in selecting chemically resistant geomembranes and implementing appropriate protective measures.
- Subsurface Conditions: Investigating subsurface conditions, such as the presence of rocks, sharp objects, or buried utilities, is essential to minimize the risk of punctures or damage during installation. Geotechnical investigations, including soil borings or geophysical surveys, can provide valuable information about subsurface conditions.
- Site Access and Logistics: Site access and logistical factors, such as proximity to transportation routes, availability of construction equipment, and space constraints, should be considered. These factors influence the ease of installation, material transportation, and construction activities, impacting the overall efficiency of the project.
Geomembrane installation methods and needs
Here are some common installation methods and needs for geomembranes:
- Preparing the Subgrade: The subgrade preparation involves clearing the site, removing vegetation, rocks, debris, and any unsuitable materials. The subgrade should be properly compacted to provide a stable base for the geomembrane.
- Anchoring and Fixing: Geomembranes often require anchoring or fixing to prevent movement or displacement. Common methods include anchor trenches, anchor trenches with backfill, anchor trenches with concrete or ballast blocks, or mechanical fasteners. The choice of anchoring method depends on site conditions, project specifications, and the type of geomembrane being installed.
- Seam Welding: Geomembrane panels are typically seamed together to create a continuous liner. The most common method is heat fusion welding, where the geomembrane panels are overlapped and heated to create a strong, watertight seam. Different welding techniques, such as hot wedge welding or extrusion welding, may be used depending on the geomembrane material.
- Quality Control and Testing: Proper quality control measures are essential during installation to ensure the integrity of the geomembrane system. This may involve visual inspections, non-destructive testing (e.g., air lance testing, spark testing), or destructive testing (e.g., peel and shear testing) to verify seam strength and overall quality.
- Protection Layers: Geomembranes often require protection layers to safeguard against punctures, abrasion, or ultraviolet (UV) degradation. Common protection layers include geotextiles, geocomposites, or concrete cover. These layers provide additional durability and extend the lifespan of the geomembrane.
- Geomembrane Repair: In case of damage or defects during installation or in-service, proper repair techniques should be employed. Repair methods may involve patching or welding the damaged area, depending on the severity and type of damage.
- Documentation and As-Built Drawings: Accurate documentation and as-built drawings help with project management, quality assurance, and future maintenance or repair activities. Detailed records of installation procedures, seam locations, and any deviations from the design specifications are important for reference and compliance purposes.
The reputation of manufacturer and supplier
The reputation of the manufacturer and supplier is an important consideration when selecting geomembranes for a project. A reputable manufacturer and supplier can provide numerous benefits, including high-quality products, reliable customer support, and adherence to industry standards.
Tips of installation and maintenance geomembrane
Installation Tips:
- Follow Manufacturer Guidelines: Always refer to the manufacturer’s installation guidelines and recommendations specific to the type of geomembrane being used. These guidelines provide detailed instructions and specifications for proper installation.
- Prepare the Subgrade: Ensure the subgrade is properly prepared by removing sharp objects, rocks, and debris. Compact the subgrade to provide a stable base for the geomembrane.
- Handle with Care: Handle geomembrane rolls or panels with care to avoid damage. Avoid dragging them across rough surfaces or sharp edges that could puncture or tear the material.
- Seam Integrity: Pay close attention to seam integrity during installation. Properly trained and experienced installers should perform seam welding or joining techniques according to industry best practices and manufacturer recommendations.
- Anchoring and Fixing: Implement appropriate anchoring and fixing techniques to prevent movement or displacement of the geomembrane. Follow manufacturer guidelines for selecting the right anchoring method based on site conditions and project requirements.
- Protection Layers: Consider using protective layers, such as geotextiles or geocomposites, to shield the geomembrane from punctures, abrasion, or UV degradation. These layers enhance the durability and lifespan of the geomembrane.
Maintenance Tips:
- Regular Inspections: Conduct regular inspections of the geomembrane system to identify any signs of damage, deterioration, or potential issues. Inspect seams, connections, anchorages, and protective layers for integrity and functionality.
- Cleaning and Debris Removal: Remove any accumulated debris, sediment, or vegetation from the geomembrane surface. Avoid using sharp tools or abrasive cleaning methods that may damage the material.
- Repair Promptly: Address any identified damage or defects promptly to prevent further deterioration. Follow the manufacturer’s guidelines for proper repair techniques, which may involve patching or welding the damaged area.
- Monitor Exposed Geomembranes: If any portion of the geomembrane is exposed to sunlight, monitor its condition and consider UV protection measures if necessary. UV degradation can weaken the material over time.
- Maintain Drainage Systems: Ensure that drainage systems, such as geocomposite drains or geosynthetic clay liners, are properly functioning to prevent excessive hydrostatic pressure and potential damage to the geomembrane.
- Keep Records: Maintain accurate records of installation details, maintenance activities, and any repairs performed. These records are valuable for future reference, warranty claims, and compliance purposes.
Conclusion
When choosing the right geomembrane, several key factors should be considered to ensure a successful and effective choice. These factors include the intended application, site-specific conditions, regulatory requirements, geomembrane material properties (such as strength, flexibility, chemical resistance), installation and maintenance considerations, manufacturer reputation, and cost-effectiveness.