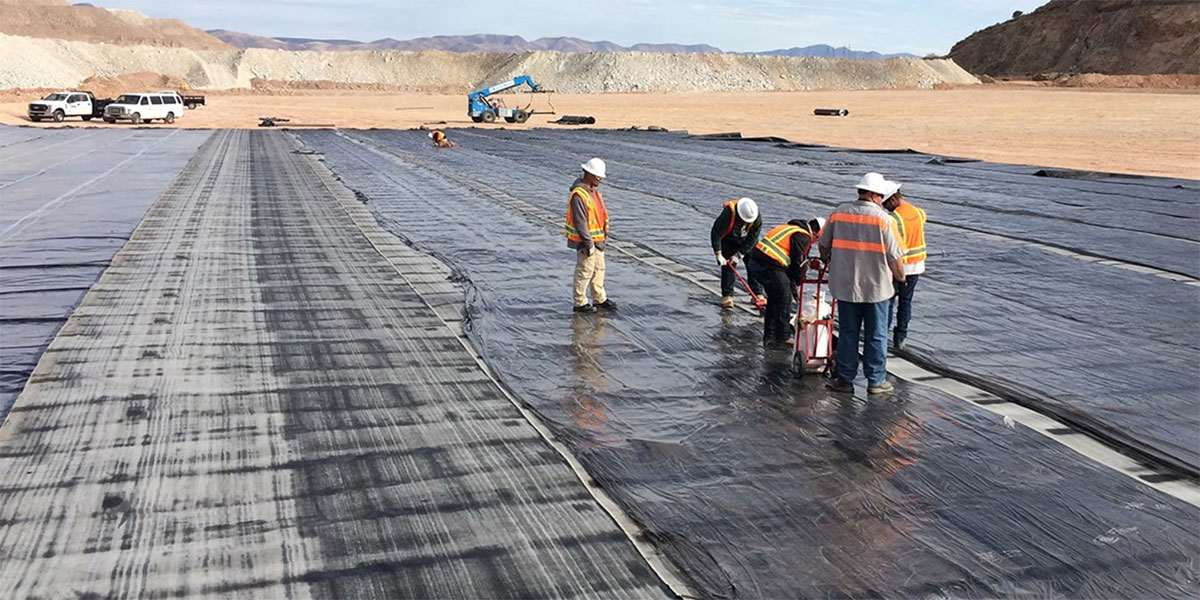
In this guide, we will explore the key benefits of BGM liners and outline best practices for their proper installation.
What is a BGM liner?
A BGM liner, or Bituminous Geomembrane liner, is a composite waterproofing system used in civil engineering and environmental protection projects. It consists of several layers, typically including a nonwoven geotextile for mechanical strength, an elastomeric bitumen binder that ensures water impermeability, and often additional reinforcement materials like glass fleece or polyester films. This multi-layered construction not only makes the liner highly resistant to punctures and tears but also provides excellent chemical resistance and long-term durability in challenging environments.
The inherent properties of BGM liners make them particularly suited for applications where long-term containment and protection against environmental elements are critical. Their low permeability helps prevent water and contaminant migration, while the robust bituminous layer and reinforcement ensure flexibility and stability under mechanical stresses. These characteristics allow BGM liners to perform well in conditions ranging from extreme temperature fluctuations to heavy traffic during installation, reducing maintenance costs and extending service life.
Widely used in industries such as mining, waste management, and water infrastructure, BGM liners serve as reliable barriers in landfills, reservoirs, canals, and tailings ponds. Their ability to conform to uneven substrates and absorb differential settlement makes them ideal for protecting the environment and ensuring the structural integrity of containment systems. The combination of ease of installation, long-term performance, and cost-effectiveness continues to drive the adoption of BGM liners in projects that require robust, durable, and versatile waterproofing solutions.
What are the benefits of BGM Liner?
BGM liners offer several benefits in various applications, particularly in water containment, environmental protection, and civil engineering projects. Here are the key advantages:
1. High Durability & Longevity
- Resistant to UV radiation and harsh weather conditions.
- Long lifespan due to strong bituminous composition.
- Withstands mechanical stress and punctures better than many polymeric liners.
2. Excellent Waterproofing Performance
- Provides superior impermeability to water and liquids.
- Prevents seepage in reservoirs, canals, and landfills.
3. Chemical & Biological Resistance
- Resistant to acids, alkalis, and hydrocarbons, making it ideal for industrial waste containment.
- Not easily degraded by microorganisms, algae, or plant roots.
4. Flexibility & Adaptability
- Can be installed over uneven surfaces without cracking.
- Remains flexible even in cold temperatures, preventing brittleness.
5. Easy Installation & Maintenance
- Can be welded or bonded for secure sealing.
- Requires minimal site preparation compared to other liners.
- Self-healing properties due to bituminous composition in some cases.
6. Strong Mechanical & Structural Performance
- Resists tearing and punctures better than HDPE liners.
- Withstands heavy loads, making it suitable for roads and landfills.
7. Cost-Effective Solution
- Lower installation and maintenance costs compared to alternative liners.
- Long service life reduces replacement and repair expenses.
What are the applications of BGM liner?
BGM liners are widely used across various industries due to their excellent waterproofing, durability, and chemical resistance. Here are the primary applications:
1. Water Containment & Management
- Reservoirs & Water Storage Tanks – Prevents water loss through seepage.
- Irrigation Canals & Channels – Ensures efficient water transport with minimal leakage.
- Ponds & Lakes – Used for artificial water bodies, fish farms, and recreational ponds.
- Stormwater & Wastewater Treatment – Provides reliable containment for effluent and treated water.
2. Environmental Protection & Waste Containment
- Landfills & Waste Disposal Sites – Acts as a barrier to prevent leachate contamination.
- Mining Operations – Used in tailings ponds and heap leach pads to contain hazardous materials.
- Oil & Chemical Spill Containment – Resists hydrocarbons, making it ideal for industrial waste sites.
3. Infrastructure & Civil Engineering
- Road Waterproofing – Protects roadbeds from water damage and enhances longevity.
- Bridge Deck Waterproofing – Prevents water infiltration, reducing corrosion risks.
- Tunnels & Underground Structures – Ensures watertight protection in underground projects.
4. Industrial & Energy Sector
- Oil & Gas Facilities – Used for secondary containment under fuel storage tanks.
- Power Plants & Cooling Ponds – Provides leak-proof lining for cooling systems.
- Desalination Plants – Ensures secure containment of saline and processed water.
5. Agricultural Applications
- Manure Lagoons & Biogas Plants – Prevents contamination from organic waste.
- Aquaculture Farms – Ensures a stable and waterproof environment for fish and shrimp farming.
Proper installation of a Bituminous Geomembrane liner ensures long-term performance, durability, and waterproofing efficiency. Below are the essential steps and expert tips to follow:
BGM liner installation steps and tips
Proper installation of a Bituminous Geomembrane liner ensures long-term performance, durability, and waterproofing efficiency. Below are the essential steps and expert tips to follow:
1. Site Preparation
- Excavation & Leveling: Clear vegetation, sharp objects, and debris. Ensure a smooth and compacted base to avoid punctures.
- Subgrade Preparation: Apply a layer of sand, geotextile, or compacted soil if needed. Ensure no standing water or mud before installation.
2. Liner Unrolling & Placement
- Positioning the Rolls: Use proper lifting equipment to avoid damage. Roll out the BGM liner in sections, allowing overlap.
- Allow for Expansion & Contraction: Leave some slack to accommodate temperature changes. Avoid stretching or pulling the liner too tightly.
3. Seaming & Welding
- Overlap Sections Properly: Maintain at least 15-20 cm (6-8 inches) of overlap between sheets. Ensure alignment before welding.
- Use Correct Welding Methods:
- Torch welding (for field seams) – Uses a propane torch to fuse bitumen layers.
- Factory pre-welded seams – Preferred for large projects to minimize field seams.
- Quality Checks: Perform visual inspection of seams. Conduct air pressure or vacuum tests to verify seal integrity.
4. Anchoring & Edge Protection
- Trench Anchoring: Place edges in anchor trenches (30-50 cm deep) to secure the liner. Backfill with compacted soil or concrete for stability.
- Ballast Weights (if required): Use sandbags or gravel to prevent wind uplift.
5. Final Inspection & Testing
- Leak Detection: Perform water testing or electrical leak detection for assurance.
- Protective Covering (if applicable): Apply soil, gravel, or geotextile layers where necessary.
Conclusion
Finally Bituminous Geomembrane (BGM) liners offer superior durability, waterproofing, and chemical resistance, making them ideal for various containment applications. Proper installation, including site preparation, secure welding, and regular inspections, ensures long-term performance and reliability.