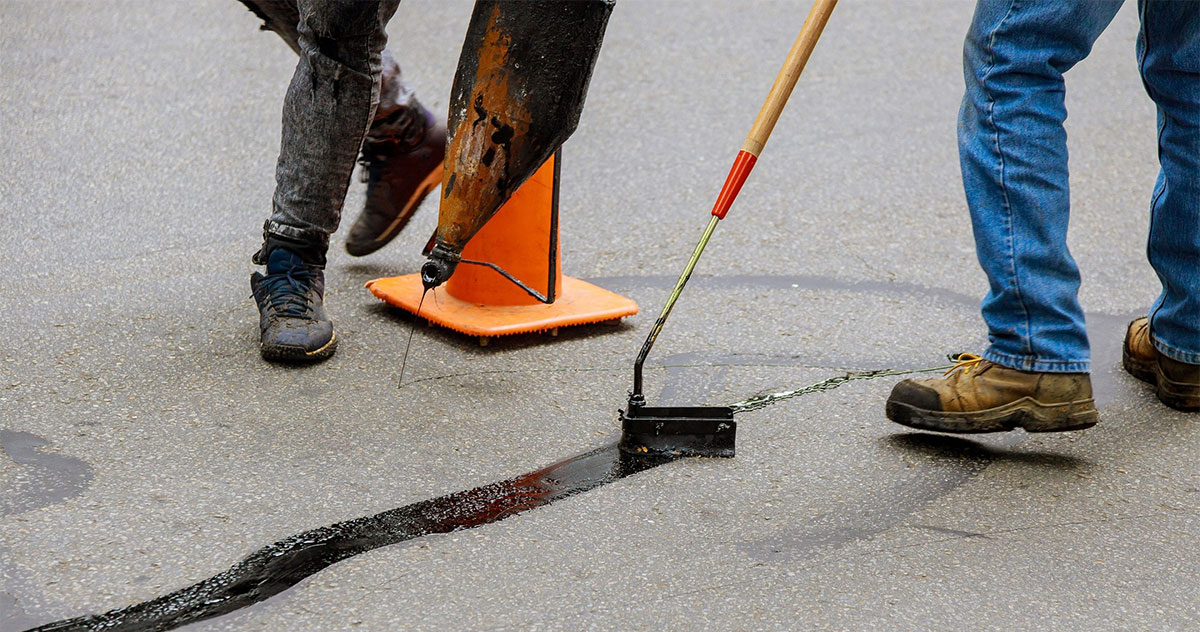
Concrete sealing is a vital process that involves applying protective coatings or incorporating geosynthetics to enhance the performance and longevity of concrete structures. By sealing concrete, it becomes more resistant to water damage, chemical deterioration, staining, and other forms of wear and tear. Understanding the different types of sealers, proper application methods, and maintenance practices is crucial for achieving optimal results in concrete sealing projects.
What does concrete sealing do?
Concrete sealing is a process that involves applying a protective coating or sealant to the surface of concrete structures, such as floors, walls, or pavements. The main purpose of concrete sealing is to enhance the durability and longevity of the concrete by providing a barrier against moisture, chemicals, stains, and other potential sources of damage.
Concrete is a porous material that can absorb water and various substances, leading to issues such as cracking, erosion, staining, and the growth of mold or mildew. By applying a sealant, the pores in the concrete are filled, reducing its permeability and preventing the ingress of moisture and contaminants.
The benefits of concrete sealing include:
- Moisture Protection: Sealing concrete helps to prevent water absorption, which can cause damage over time. It protects against issues like cracking, spalling, and deterioration caused by freeze-thaw cycles.
- Stain Resistance: A sealed concrete surface is less prone to staining from spills, oils, chemicals, and other substances. The sealant acts as a protective barrier, making it easier to clean and maintain the appearance of the concrete.
- Enhanced Durability: Concrete sealants can improve the overall strength and durability of the concrete, making it more resistant to abrasion, wear, and surface damage.
- Dust Reduction: Sealing concrete reduces the release of concrete dust, which can be a concern in areas with high foot traffic or where dust particles can become airborne.
- Improved Aesthetics: Depending on the type of sealant used, concrete sealing can enhance the appearance of the surface by providing a glossy or matte finish. It can also enhance the color and vibrancy of decorative concrete.
- Protection against Chemicals: Sealants can provide resistance against chemical spills or exposure, preventing damage and maintaining the integrity of the concrete surface.
Read more: Roof Sealing Using Geosynthetics
When should you seal concrete?
Concrete should be sealed at an appropriate time to ensure optimal protection and longevity. The timing of concrete sealing depends on the type of concrete and the specific project. Here are some general guidelines on when to seal concrete:
- New Concrete: For newly poured concrete, it is generally recommended to wait for it to fully cure before sealing. This typically takes around 28 days, but it can vary depending on factors such as concrete mix, weather conditions, and thickness. Sealing too early can trap moisture within the concrete and hinder proper curing.
- Existing Concrete: If you have existing concrete that has never been sealed, it is important to clean and prepare the surface before applying a sealant. The concrete should be free from dirt, stains, and any previous coatings. It is typically best to seal existing concrete when weather conditions are dry and temperatures are moderate for optimal application and curing.
- Decorative Concrete: Decorative concrete surfaces, such as stamped or stained concrete, may require specific timing for sealing. It is essential to follow the manufacturer’s recommendations or consult with a professional to determine the appropriate time to seal decorative concrete. This is typically after the surface has fully cured and any coloring or staining processes have been completed.
- Maintenance and Reapplication: Over time, the effectiveness of a concrete sealant may diminish due to wear, weathering, or exposure to chemicals. Regular maintenance and reapplication of sealant are necessary to ensure continued protection. The frequency of resealing depends on factors such as the type of sealant used, the level of traffic or exposure, and the specific conditions of the concrete surface. It is advisable to monitor the condition of the concrete and reseal as needed.
Concrete sealing types and methods
There are various types of concrete sealers available, each with its own characteristics and suitable applications. The choice of sealer depends on factors such as the desired level of protection, the type of concrete surface, and the specific project requirements. Here are some common types of concrete sealers and methods of application:
- Penetrating Sealers: Also known as impregnating sealers, these sealers penetrate into the concrete surface and react with the minerals to form a protective barrier within the pores. They provide excellent protection against moisture, stains, and freeze-thaw damage while allowing the concrete to retain its natural appearance. Penetrating sealers are typically applied using spray, roller, or brush methods.
- Acrylic Sealers: Acrylic sealers form a thin protective film on the surface of the concrete. They are available in both water-based and solvent-based formulations. Acrylic sealers offer good UV resistance, durability, and resistance to chemicals and abrasion. They can enhance the appearance of the concrete by providing a glossy or matte finish. Acrylic sealers are commonly applied using a roller or sprayer.
- Epoxy Sealers: Epoxy sealers provide a strong and durable protective coating on the concrete surface. They are resistant to chemicals, stains, and abrasion, making them suitable for high-traffic areas. Epoxy sealers offer a glossy finish and can enhance the concrete’s appearance. They are typically applied in multiple coats using a roller or squeegee.
- Polyurethane Sealers: Polyurethane sealers provide a tough and flexible protective coating. They offer excellent resistance to chemicals, UV rays, and abrasion. Polyurethane sealers are commonly used for outdoor applications or areas subjected to heavy wear and tear. They can be applied using a roller or sprayer.
- Decorative Sealers: These sealers are specifically designed for decorative concrete surfaces, such as stamped or stained concrete. They enhance the color, vibrancy, and visual appeal of the concrete while providing protection. Decorative sealers may include acrylic, epoxy, or polyurethane formulations, depending on the desired aesthetics and level of protection.
The application methods for concrete sealers can include:
- Spray: Using a sprayer, the sealer is evenly applied onto the concrete surface. This method is suitable for larger areas or when a thin, uniform coat is desired.
- Roller: A roller is used to apply the sealer onto the concrete surface. It is an effective method for both small and large areas.
- Brush: A brush is used to manually apply the sealer onto the concrete surface, typically for smaller areas or detailed applications.
Read more: Concrete Tanks Sealing Methods
Concrete sealing process
The concrete sealing process typically involves the following steps:
- Surface Preparation: Thoroughly clean the concrete surface to remove any dirt, debris, stains, or previous coatings. Use a pressure washer, scrub brush, or suitable cleaning solution to ensure the surface is free from contaminants. Allow the concrete to dry completely before proceeding.
- Patching and Repair (if needed): Inspect the concrete for any cracks, spalling, or other damage. Repair these areas using suitable concrete patching materials and follow the manufacturer’s instructions. Allow the repairs to cure before moving on to the next step.
- Selecting the Sealer: Choose the appropriate type of concrete sealer based on the desired level of protection, appearance, and specific project requirements. Consider factors such as the type of concrete surface, exposure to chemicals or UV radiation, and the intended use of the area.
- Testing and Application: Before applying the sealer to the entire surface, it is recommended to perform a small test patch in an inconspicuous area. This allows you to evaluate the sealer’s compatibility, appearance, and coverage rate on the specific concrete surface.
- Applying the Sealer: Follow the manufacturer’s instructions for the specific sealer being used. Typically, the sealer is applied using a sprayer, roller, or brush. Ensure even and consistent coverage, applying multiple thin coats if necessary. Take care to avoid puddling or excess buildup of the sealer.
- Drying and Curing: Allow the sealer to dry and cure according to the manufacturer’s recommendations. This typically involves avoiding foot or vehicle traffic on the sealed surface for a specific period. Keep in mind that drying and curing times can vary depending on factors such as temperature, humidity, and the type of sealer used.
- Maintenance and Reapplication: Regularly maintain the sealed concrete surface by cleaning it with mild detergents and avoiding harsh chemicals or abrasive cleaners. Monitor the condition of the sealer over time and reapply as needed to ensure continued protection and performance.
Read more: Everything About Pool Sealing
Concrete sealing using geosynthetics
The process of concrete sealing using geosynthetics typically involves the following steps:
- Surface Preparation: Prepare the concrete surface by cleaning it thoroughly and ensuring it is free from dirt, debris, and loose particles. Repair any cracks or damage in the concrete as necessary.
- Geosynthetic Selection: Choose the appropriate type of geosynthetic material based on the specific sealing requirements. Common types of geosynthetics used for concrete sealing include geomembrane sheets, geotextiles, and geocomposite sheets. Consider factors such as the desired level of waterproofing, compatibility with the concrete, and the environmental conditions of the project site.
- Geosynthetic Placement: Install the geosynthetic material onto the prepared concrete surface according to the manufacturer’s guidelines. The specific placement method may vary depending on the type of geosynthetic being used. Geomembranes, for example, are typically laid over the concrete, while geocomposites may be embedded within the concrete or sandwiched between concrete layers.
- Joining and Seaming: Ensure proper joining and seaming of the geosynthetic materials to create a continuous barrier. Various methods, such as heat welding, adhesive bonding, or mechanical fastening, may be employed depending on the type of geosynthetic and manufacturer recommendations.
- Concrete Application: Pour or apply the concrete mixture over the geosynthetic layer, ensuring proper compaction and consolidation. The geosynthetic works as a barrier, preventing water penetration and enhancing the overall integrity of the concrete structure.
- Curing and Maintenance: Follow standard curing practices for the concrete, allowing it to properly set and gain strength. Regular maintenance of the sealed concrete structure is essential to ensure long-term effectiveness. Inspect for any signs of damage or deterioration and address them promptly to maintain the integrity of the sealing system.
Conclusion
In conclusion, concrete sealing is a crucial process that enhances the durability, protection, and longevity of concrete structures. By applying suitable sealers or incorporating geosynthetics, concrete can be safeguarded against moisture infiltration, chemical damage, staining, and other forms of deterioration.