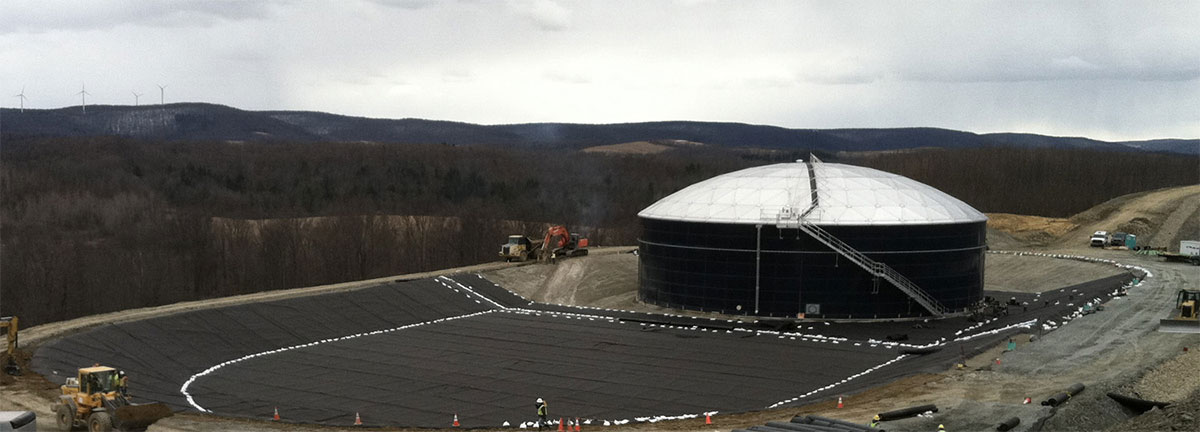
In the oil and gas industry, geosynthetics play a vital role in addressing engineering challenges. These versatile materials are utilized for various applications, including containment systems, foundation reinforcement, and slope stabilization, contributing to enhanced environmental protection and infrastructure integrity. In this article we discuss about geosynthetics in the oil and gas industry.
Geosynthetics applications in pad liners
Geosynthetics offer several advantages when used in pad liners, including improved stability, durability, and environmental protection. Here are some key applications of geosynthetics in pad liners:
- Geomembranes: Geomembranes sheet are impermeable plastic sheets or liners used to contain liquids and prevent them from infiltrating the underlying soil. In pad liners, geomembranes act as a barrier to protect the environment from potentially harmful substances. High-density polyethylene (HDPE) and linear low-density polyethylene (LLDPE) are common geomembrane materials due to their chemical resistance and durability.
- Geotextiles: Geotextiles are permeable fabrics that are placed in contact with the soil and provide functions such as filtration, separation, and reinforcement. In pad liners, geotextiles are often used as a protective layer between the geomembrane and the soil. They help prevent punctures or abrasions to the geomembrane, enhance drainage, and promote soil-geomembrane interaction.
- Geocomposites: Geocomposite sheets are combinations of different geosynthetic materials, such as geotextiles and geomembranes, into a single product. In pad liners, geocomposites can offer a combination of functions, such as providing both separation and filtration properties. For example, a geocomposite may consist of a geotextile layer to protect the geomembrane and a geomembrane layer to contain liquids.
- Geogrids: Geogrids are geosynthetic materials used to reinforce soil and enhance its stability. In some pad liner applications, geogrids may be employed to improve the overall structural integrity of the liner system. By reinforcing the soil, geogrids can help distribute loads more evenly and reduce the potential for settlement.
- GCLs (Geosynthetic Clay Liners): GCLs consist of a layer of bentonite clay sandwiched between two geotextiles. They are often used in pad liners to provide both a low-permeability barrier and additional reinforcement. GCLs swell when in contact with water, creating a tight seal that enhances their ability to contain liquids.
- Erosion Control: Geosynthetics can also play a role in erosion control on the slopes of pad liners. Geotextiles, for instance, can be used to stabilize soil and prevent erosion, ensuring the long-term integrity of the liner system.
Geosynthetics usage in secondary containment
Secondary containment refers to the protective measures implemented to prevent the escape of hazardous substances in the event of a primary containment system failure. Here are some key applications of geosynthetics in secondary containment:
- Geomembranes: Geomembranes are impermeable plastic liners that act as a barrier to contain liquids. In secondary containment systems, geomembranes are often used as the primary liner material. Materials like high-density polyethylene (HDPE), linear low-density polyethylene (LLDPE), and reinforced geomembranes are commonly employed due to their chemical resistance and durability.
- Geotextiles: Geotextiles are permeable fabrics that can be used in conjunction with geomembranes to enhance the performance of secondary containment systems. Placing geotextiles beneath or above geomembranes can provide protection against punctures, abrasions, and soil erosion. Geotextiles also aid in drainage and filtration within the containment structure.
- Geocomposites: Geocomposites combine different geosynthetic materials into a single product, offering multiple functions within a secondary containment system. For example, a geocomposite might include a geomembrane layer for liquid containment and a geotextile layer for protection and filtration. This integrated approach improves the overall performance of the containment system.
- Geosynthetic Clay Liners (GCLs): GCLs, consisting of a layer of bentonite clay between geotextiles, are used in secondary containment systems to provide both a low-permeability barrier and additional protection. GCLs can swell when in contact with liquids, enhancing their ability to seal and contain hazardous substances.
- Leak Detection and Monitoring: Geosynthetics can also be integrated into secondary containment systems for leak detection and monitoring. Geomembranes with embedded sensors or liners designed for visual inspection can help identify potential leaks early, allowing for prompt corrective action.
- Slope Reinforcement: In some cases, geosynthetics like geogrids may be used to reinforce slopes within secondary containment systems. Reinforcing the soil structure with geogrids can enhance stability and prevent erosion, ensuring the long-term effectiveness of the containment measures.
- Repair and Maintenance: Geosynthetics simplify repair and maintenance activities in secondary containment systems. The modular nature of many geosynthetic materials allows for relatively easy replacement or repair of damaged sections, minimizing downtime and potential risks.
In-ground and above-ground impoundment
In-ground and above-ground impoundments are engineered structures designed to contain and manage liquids, often associated with industrial processes, waste storage, or water management. Both types of impoundments serve specific purposes and come with advantages and challenges.
In-Ground Impoundments:
- Design and Construction:
- Excavation: In-ground impoundments are typically excavated into the ground to create a basin or pit for liquid containment.
- Liner Systems: Geosynthetic liners, such as geomembranes and geosynthetic clay liners (GCLs), are often used to line the excavated area, preventing the leakage of liquids into the surrounding soil.
- Applications:
- Waste Storage: In-ground impoundments are commonly used for storing liquid waste from industrial processes, such as mining tailings or chemical effluents.
- Water Retention: They can also be used for water retention or detention in stormwater management.
- Advantages:
- Cost-Effective: In-ground impoundments can be more cost-effective to construct initially.
- Integration with Topography: They can be designed to integrate with the natural topography of the site.
- Challenges:
- Groundwater Interaction: The risk of groundwater contamination exists, requiring careful consideration of liner systems.
- Maintenance Challenges: Access and maintenance of liners can be challenging once the impoundment is in use.
Above-Ground Impoundments:
- Design and Construction:
- Constructed Structures: Above-ground impoundments are constructed above the natural ground level using materials such as concrete, steel, or synthetic membranes.
- Containment Walls: They have containment walls to prevent spills and leaks.
- Applications:
- Liquid Storage: Commonly used for storing liquids in various industries, including oil and gas, chemicals, and agriculture.
- Emergency Spill Containment: Above-ground impoundments can serve as emergency spill containment structures.
- Advantages:
- Ease of Inspection: Above-ground impoundments are generally easier to inspect and maintain.
- Reduced Environmental Impact: Reduced risk of groundwater contamination compared to in-ground impoundments.
- Challenges:
- Structural Integrity: The structural integrity of containment walls is crucial to prevent leaks or breaches.
- Aesthetics: Above-ground impoundments may have visual and aesthetic impacts, especially in sensitive or residential areas.
Considerations for Both Types:
- Regulatory Compliance: Both in-ground and above-ground impoundments must comply with environmental regulations, which may dictate liner specifications, monitoring requirements, and emergency response plans.
- Geosynthetics in Liners: Both types may use geosynthetic liners, but the selection and design depend on factors such as the type of liquid being stored, the geological conditions of the site, and regulatory requirements.
- Maintenance and Monitoring: Regular maintenance and monitoring are critical for both types to ensure the integrity of the containment system and to detect potential issues promptly.
Floating covers
Floating covers, also known as floating membranes or blankets, are specialized geosynthetic materials designed to float on the surface of liquids, providing various benefits such as evaporation reduction, temperature control, and the prevention of environmental contamination. These covers are commonly used in liquid storage facilities, wastewater treatment ponds, and other applications where the control of liquid exposure is critical.
Geosynthetics usage in oil tanks
Here are some key applications of geosynthetics in oil tanks:
- Secondary Containment Liners:
- Geomembranes: Geomembranes are impermeable liners used in secondary containment systems to prevent the leakage of oil and other hazardous materials into the environment. High-density polyethylene (HDPE) and other chemically resistant geomembranes are often used to line the base and walls of the containment area.
- Leak Detection and Monitoring:
- Geosynthetic Liners with Sensors: Some geomembranes come with built-in sensors or leak detection systems. These sensors can detect changes in pressure, temperature, or the presence of oil, helping to identify and locate potential leaks early on.
- Geomembrane Floating Covers: Floating covers made of geomembranes can be used to reduce evaporation losses and prevent oil spills. These covers are particularly useful in open-topped tanks where exposure to the elements is a concern.
- Geotextiles: Geotextiles may be used in the construction of bunds or berms around oil storage tanks. These materials provide reinforcement and stability to the soil structure, preventing erosion and aiding in the containment of oil in case of a spill.
- Geotextiles and Geogrids: Geotextiles and geogrids can be used for erosion control around the tank area. They help stabilize the soil, prevent soil erosion, and protect against the formation of ruts and channels caused by runoff.
- Geogrids: Geogrids may be used to reinforce the foundation of the tank, providing additional support and stability to the structure. This is especially important in areas with weak or expansive soils.
- Geosynthetics for Slope Stability: In areas where tanks are located on slopes, geosynthetics like geocells or geogrids can be used to enhance slope stability, prevent soil erosion, and protect against potential landslides.
- Geocomposites: Geocomposites that incorporate cathodic protection materials can be used to provide additional corrosion resistance to the tank. This is crucial for maintaining the structural integrity of the tank and preventing leaks.
- Geomembranes as Vapor Barriers: Geomembranes can be used as vapor barriers to prevent the migration of volatile organic compounds (VOCs) or other harmful gases from the stored oil into the surrounding environment.
- Geosynthetic Solutions for Repair: Geosynthetics can be employed in rehabilitation projects to repair or reinforce the structural elements of existing oil tanks, extending their service life.
- Floating Covers
- Bunds and Berms
- Erosion Control
- Tank Foundation Reinforcement
- Slope Protection
- Cathodic Protection
- Vapor Barriers
- Rehabilitation and Repair
The advantages of using composite geomembrane in oil fields
Composite geomembranes, which consist of multiple layers of different geosynthetic materials, offer several advantages when used in oil fields for containment and environmental protection. Here are some key advantages of using composite geomembranes in oil fields:
- Enhanced Barrier Properties:
- Composite geomembranes typically combine different materials, such as a high-density polyethylene (HDPE) layer and a geosynthetic clay liner (GCL) layer. This combination enhances the overall barrier properties of the geomembrane, providing improved resistance to the permeation of oil and other contaminants.
- Chemical Resistance:
- The composite structure allows for the selection of specific materials with high chemical resistance. This is important in oil fields where the stored substances may include corrosive or chemically aggressive materials. The geomembrane can be customized to resist degradation from exposure to hydrocarbons, acids, and other chemicals.
- Incorporating layers with different properties, such as a reinforced geomembrane layer, can enhance the puncture resistance of the composite geomembrane. This is particularly beneficial in environments where the geomembrane may be subjected to mechanical stress or where there is a risk of sharp objects causing damage.
- Geosynthetic reinforcements, such as geotextiles or geogrids, can be included in the composite structure to enhance stability on slopes. This is especially relevant in oil fields where containment structures may be constructed on uneven terrain.
- Composite geomembranes can be designed to be flexible and conform to the shape of the containment area. This flexibility is advantageous when dealing with irregularly shaped storage facilities or when conforming to the contours of the underlying terrain.
- UV-resistant components can be included in the composite geomembrane to protect against the degrading effects of sunlight. This is crucial in outdoor oil field applications where prolonged exposure to sunlight can lead to material degradation.
- Composite geomembranes are often prefabricated in factory conditions, leading to consistent quality and ease of installation. The prefabricated nature of these liners can result in faster and more efficient installation in oil field projects.
- Some composite geomembranes can be equipped with leak detection technologies, such as embedded sensors or monitoring systems. This allows for early detection of potential leaks or breaches, contributing to the overall safety of oil containment systems.
- Composite geomembranes can be customized based on the specific requirements of the oil field site, considering factors such as soil conditions, climate, and the types of liquids being stored.
- The combination of different materials in composite geomembranes often results in a product with excellent durability and resistance to environmental stressors, ensuring a longer service life for containment structures in oil fields.
- Increased Puncture Resistance
- Improved Stability on Slopes
- Flexibility and Conformability
- Resistance to UV Degradation
- Ease of Installation
- Leak Detection Capabilities
- Customization for Site-Specific Conditions
- Long-Term Durability
Conclusion
In the oil and gas industry, geosynthetics find diverse applications such as secondary containment liners, tank foundation reinforcement, slope stabilization, and leak detection systems. Their use enhances environmental protection, containment integrity, and overall infrastructure performance, making geosynthetics crucial for addressing engineering challenges in the oil and gas sector.