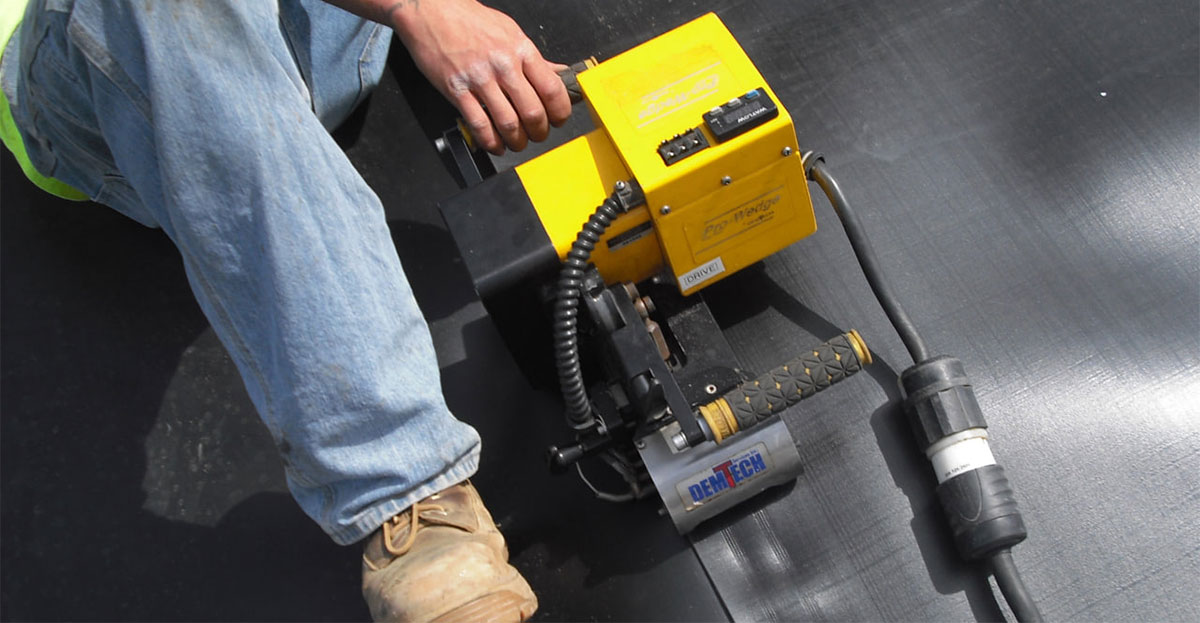
Geomembrane welding is a crucial process in industries like waste management, agriculture, and construction, where a reliable waterproof barrier is needed. In this blog post we provide a comprehensive guide to geomembrane welding.
What is the purpose of welding geomembranes?
Welding geomembranes is essential for creating a continuous, impermeable barrier that prevents the migration of liquids and gases. By fusing individual sheets at a molecular level through thermal or chemical methods, welding eliminates gaps and weak points that could otherwise lead to leakage. This seamless integration is crucial in applications such as landfill liners, reservoirs, and hazardous waste containment, where even small breaches can result in environmental contamination.
In addition to providing environmental protection, the welding process enhances the structural integrity and durability of the geomembrane system. A properly executed weld retains nearly the full tensile strength of the original material, ensuring that the joint withstands mechanical stresses, temperature fluctuations, and long-term aging. This robust performance minimizes maintenance needs and prolongs the lifespan of the installation, contributing to a cost-effective and reliable barrier system.
Which welding tools are used for geomembrane?
Common welding tools for geomembrane installations include a variety of thermal and chemical devices designed to fuse overlapping sheets at the molecular level. For example, hot-air welders are commonly used—they apply heated air to soften the material surfaces before pressing them together, making them suitable for a range of geomembrane materials like PVC, HDPE, and LLDPE. Extrusion welders are another popular choice; these machines force a welding rod made from the same resin as the geomembrane into the joint, forming a molten bead that creates a strong bond as it cools. In addition, wedge welders—which are typically handheld—utilize a heated metal wedge to melt the seam area before applying pressure with rollers to achieve a uniform weld.
Other specialized tools include equipment for chemical welding, where solvents are applied to soften the geomembrane surfaces (primarily used for PVC and urethane-based membranes), and, in some cases, ultrasonic welding devices which use high-frequency vibrations to join the material. Modern, integrated welding machines often come as dual-drive, self-propelled units that not only perform the weld but also facilitate on-site seam testing to ensure quality and continuity. This diverse toolkit allows engineers to select the most appropriate method based on material type, environmental conditions, and project requirements.
How is geomembrane welded? Actions required
Welding geomembrane involves fusing sheets of material (such as HDPE, LLDPE, PVC, or other synthetic membranes) to create a seamless and impermeable barrier. The process typically involves the following steps:
1. Preparation
- Site Preparation: Ensure the welding area is clean, dry, and free of debris.
- Surface Cleaning: Remove dust, dirt, and moisture from the geomembrane edges to ensure a strong weld.
- Overlap Alignment: Align the geomembrane sheets with the required overlap (usually 50-100 mm, depending on the welding method).
2. Welding Methods
There are three primary welding techniques for geomembranes:
A. Hot Wedge Welding (Preferred for HDPE & LLDPE)
- Uses a heated wedge to soften the geomembrane surfaces.
- Pressure is applied to fuse the materials together.
- Creates a dual-track weld with an air channel for testing.
B. Hot Air Welding (For thinner or flexible materials like PVC)
- Uses a stream of hot air to soften the geomembrane.
- A roller presses the sheets together to form a bond.
- Suitable for small repairs and intricate welds.
C. Extrusion Welding (For repairs & detailed work)
- A plastic rod is melted and extruded into the seam to bond the sheets.
- Used for T-joints, pipe penetrations, or patch repairs.
3. Testing & Quality Control
- Visual Inspection: Check for uniformity, smoothness, and complete fusion.
- Air Channel Testing: For dual-track welds, compressed air is injected into the channel to check for leaks.
- Vacuum Box Testing: A vacuum box is applied to the seam with soapy water to detect leaks (for single-track welds).
- Destructive Testing: A sample is cut and tested for shear and peel strength using a field tensiometer.
4. Final Checks & Documentation
- Ensure all seams are tested and verified.
- Record welding parameters (temperature, speed, pressure) for quality assurance.
- Any defects should be repaired immediately with extrusion welding.
Geomembrane welding machine and its different types
Geomembrane welding machines are essential tools used in the installation of geosynthetic products for various applications such as landfills, mining ponds, and water containment facilities. There are several types of geomembrane welding machines, each designed for specific materials and project requirements:
Hot wedge welding machines
These machines use a heated wedge to melt and fuse the surfaces of geomembrane liners. They are the most common type used in geomembrane installation, offering high production rates and consistent welding quality. Hot wedge welders are ideal for large-scale projects like extensive commercial tasks, mining operations, and large landfills.
Extrusion welding machines
Extrusion welders use a heated extruder to melt the geomembrane surfaces and extrude a molten welding rod to form a welded joint. These machines are particularly useful for adding material to a weld, providing additional strength in areas requiring repair or where membrane seams overlap. They are commonly used in projects that demand high structural integrity in welds, such as landfills.
Hot air welding machines
Hot air welders use a flow of heated air to soften and melt the surface of the geomembrane. These machines are versatile, portable, and suitable for both thick and thin membranes. They are commonly used for minor repairs, small projects, and in limited-space environments like underground storage tanks.
Vibrating knife cutting mchines
While not strictly a welding machine, vibrating knife cutting machines are often used in conjunction with welding equipment. They utilize a vibrating blade to cut through geomembranes, ensuring precise and clean cuts for complex designs or custom fittings.
Each type of geomembrane welding machine has its specific applications and advantages, and the choice depends on factors such as project scale, material compatibility, terrain conditions, and specific project demands.
Several things to pay attention to when welding geomembrane
When welding geomembrane, several critical factors must be considered to ensure a strong, leak-proof, and durable weld. Here are the key aspects to pay attention to:
1. Environmental Conditions
- Temperature: Ideal ambient temperature for welding is usually between 5°C and 40°C. Extreme cold can make the material brittle, while excessive heat can cause overheating.
- Wind Speed: Strong winds can cool down the weld area too quickly, causing weak bonds. Use wind barriers if necessary.
- Humidity & Moisture: Wet or damp surfaces prevent proper fusion. Ensure the geomembrane is dry before welding.
2. Surface Preparation
- Cleanliness: Remove dirt, dust, and moisture from the welding area to prevent contamination.
- Overlap Alignment: Ensure proper overlap (typically 50-100 mm) for a strong joint. Uneven overlaps can cause weak seams.
- Material Compatibility: Ensure both sheets are made of the same material type and thickness for uniform fusion.
3. Welding Parameters
- Temperature: Proper heat settings depend on material type and thickness.
- HDPE: 200-450°C (depends on conditions)
- PVC: 200-300°C
- Pressure: Sufficient pressure must be applied to ensure bonding without burning the material.
- Speed: Welding speed should be adjusted to match the temperature and thickness (too fast = weak bond, too slow = burns or deformations).
4. Equipment & Tools
- Calibrated Welding Machines: Use reliable hot wedge, hot air, or extrusion welders with accurate temperature and pressure settings.
- Power Supply Stability: Ensure consistent power to avoid fluctuations in welding temperature.
- Backup Equipment: Keep spare parts (wedge heaters, nozzles) on hand to prevent delays.
5. Seam Quality & Testing
- Visual Inspection: Check for uniformity, smoothness, and complete fusion.
- Air Pressure Test: For dual-track welds, inject air between the tracks to check for leaks.
- Vacuum Box Test: Apply vacuum and soapy water to detect leaks in single welds.
- Destructive Testing: Cut and test samples for shear and peel strength.
6. Worker Skill & Training
- Ensure operators are trained to handle different geomembrane materials and welding conditions.
- Conduct test welds before starting major projects.
Conclusion
Geomembrane welding is a critical process that ensures a strong, leak-proof barrier for containment applications. Proper surface preparation, controlled environmental conditions, accurate welding parameters, and thorough quality testing are essential for achieving durable seams. Using the right equipment and trained personnel helps prevent failures and extends the lifespan of the installation.