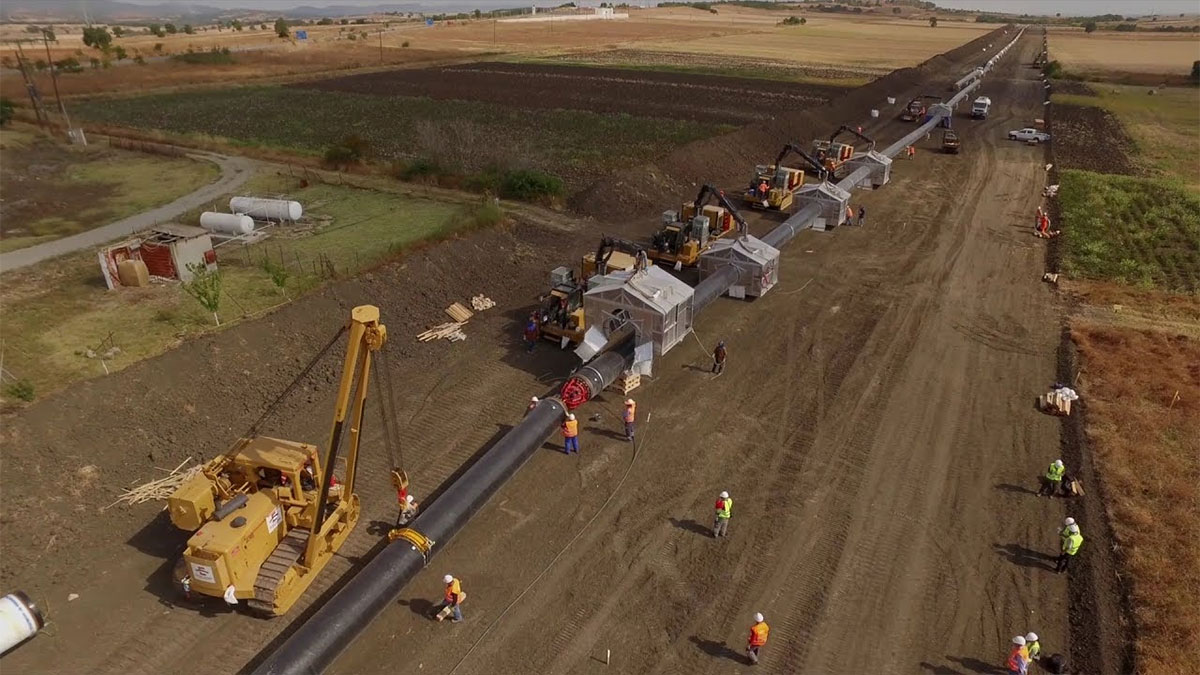
Pipeline construction is a systematic process involving route selection, surveying, trenching, welding, and testing to establish a safe and efficient means of transporting fluids like oil, gas, or water. This intricate process addresses environmental considerations, regulatory approvals, and utilizes specialized equipment for tasks such as excavation, welding, and coating.
What are the pipeline construction steps?
The construction of a pipeline involves several key steps to ensure the safe and efficient transportation of fluids (such as oil, gas, or water) from one point to another. Here are the general steps in the pipeline construction process:
- Route Selection:
- Conduct a thorough feasibility study to identify the best route for the pipeline.
- Consider environmental, social, and economic factors.
- Obtain necessary permits and approvals from regulatory authorities.
- Surveying and Staking:
- Conduct detailed surveys to determine the exact path of the pipeline.
- Mark the pipeline route on the ground, including any necessary right-of-way.
- Clearing and Grading:
- Clear the right-of-way by removing vegetation, rocks, and other obstacles.
- Grade the land to create a smooth and even surface for construction.
- Trenching:
- Excavate a trench along the pipeline route to accommodate the pipeline.
- Ensure the trench is deep enough to cover the pipeline and provide stability.
- Stringing:
- Bring the pipes to the construction site and lay them along the right-of-way.
- Check the alignment and weld the pipes together to create the pipeline.
- Bending and Coating:
- Bend the pipes as necessary to follow the curvature of the pipeline route.
- Apply a protective coating to the pipes to prevent corrosion.
- Lowering-In or Stringing:
- Lower the welded pipe strings into the trench.
- Ensure proper alignment and make any necessary adjustments.
- Welding:
- Weld the individual pipe sections together to create a continuous pipeline.
- Conduct non-destructive testing to ensure the integrity of the welds.
- Backfilling:
- Fill the trench with the excavated soil, compacting it to provide stability.
- Perform restoration work on the right-of-way, including reseeding and replanting.
- Testing:
- Conduct various tests, such as hydrostatic testing, to ensure the pipeline’s integrity.
- Check for leaks and ensure that the pipeline can withstand the operational pressure.
- Commissioning:
- Prepare the pipeline for operation by flushing and cleaning it.
- Integrate the pipeline into the overall system and start transporting the intended fluid.
- Monitoring and Maintenance:
- Implement a monitoring system to continuously assess the pipeline’s performance.
- Establish a regular maintenance program to address any issues and ensure long-term reliability
What are the pipeline construction methods?
Pipeline construction methods vary depending on factors such as the type of pipeline, terrain, environmental considerations, and project requirements. Here are some common pipeline construction methods:
- Open Trench Construction:
- Description: This is the traditional method where a trench is excavated along the pipeline route, and the pipeline is laid in the trench.
- Application: Suitable for various terrains and pipeline types.
- Considerations: Environmental impact, soil conditions, and the need for backfilling and land restoration.
- Trenchless Construction:
- Description: Trenchless methods are used to install pipelines without continuous trenches. This includes methods like horizontal directional drilling (HDD), microtunneling, and auger boring.
- Application: Useful in urban areas, under rivers, and in environmentally sensitive locations.
- Considerations: Higher upfront costs but reduced environmental impact and disruption.
- S-lay and J-lay Installation (Offshore Pipelines):
- Description: Common in offshore pipeline construction, S-lay involves laying the pipeline in a continuous manner on the seabed, while J-lay involves constructing the pipeline in a vertical manner and lowering it to the seabed.
- Application: Used for underwater pipelines in offshore oil and gas fields.
- Considerations: Depth of water, seabed conditions, and installation vessel capabilities.
- Pipe Jacking:
- Description: In this trenchless method, pipes are pushed or jacked through the soil using a specialized machine.
- Application: Suitable for short distances in urban areas, beneath roads, and other structures.
- Considerations: Limited to certain soil conditions, and requires careful monitoring.
- Screw Auger Boring:
- Description: Augers are used to bore a hole for the pipeline, and the pipe is installed as the auger is removed.
- Application: Suitable for installing small-diameter pipelines in stable soil conditions.
- Considerations: Limited to relatively short distances, and may not be suitable for all soil types.
- Tow-in Installation:
- Description: Common in the offshore industry, where a pipeline is prefabricated and then towed into place.
- Application: Used for installing pipelines in deepwater or challenging seabed conditions.
- Considerations: Requires specialized vessels and careful planning.
- Hot Tapping:
- Description: This method involves making a connection to an existing pressurized pipeline without interrupting its flow.
- Application: Used for making tie-ins, repairs, or installing new branches on an operational pipeline.
- Considerations: Requires specialized equipment and careful safety measures.
- Slip-lining:
- Description: A new pipeline is inserted into an existing one, providing a cost-effective method for rehabilitation or upgrading.
- Application: Used for rehabilitating aging or corroded pipelines.
- Considerations: Requires careful sizing and compatibility between old and new pipelines.
Pipeline construction equipment list
Pipeline construction involves the use of various specialized equipment to carry out tasks such as trenching, welding, bending, and testing. The specific equipment needed can vary depending on factors like the type of pipeline, terrain, and construction methods. Here is a general list of equipment commonly used in pipeline construction:
- Excavators:
- Used for digging trenches and excavating the pipeline route.
- Backhoes:
- Useful for digging smaller trenches and for more precise excavation work.
- Trenchers:
- Designed specifically for creating trenches of consistent depth and width.
- Pipe Layers:
- Specialized equipment for laying and positioning pipes in the trench.
- Welding Machines:
- Includes various types such as stick, MIG, and TIG welders for joining pipe segments.
- Pipe Benders:
- Used to bend pipes to match the curvature of the pipeline route.
- Coating Equipment:
- Applies protective coatings to the pipes to prevent corrosion.
- Pipe Cutting Equipment:
- Cuts pipes to the required lengths and angles.
- Welding Tractors:
- Automated machines that move along the pipe during welding, ensuring consistent weld quality.
- Cranes:
- Lift and position heavy materials, pipes, and equipment.
- Side Booms:
- Specialized heavy equipment for lifting and moving pipes during pipeline construction.
- Compactors:
- Compacts soil during backfilling to provide stability.
- Hydrostatic Test Pumps:
- Used for conducting hydrostatic testing to check the integrity of the pipeline.
- Surveying Equipment:
- Includes total stations, GPS units, and other tools for accurate mapping and layout.
- Horizontal Directional Drilling (HDD) Rigs:
- Used for trenchless installation of pipelines in areas where open trenching is not feasible.
- Vacuum Excavators:
- Excavates soil using high-pressure water and then vacuums up the debris, minimizing damage to underground utilities.
- Concrete Mixers:
- Used for preparing concrete for structures such as pipeline supports.
- Blasting Equipment:
- Used for rock removal and preparation in areas with challenging terrain.
- Pigging Equipment:
- Devices known as “pigs” used for cleaning, inspecting, and maintaining pipelines.
- Test Equipment:
- Instruments for various tests, including pressure testing, X-ray inspection, and ultrasonic testing.
- Safety Equipment:
- Personal protective equipment (PPE), safety barriers, and other tools to ensure a safe working environment.
How long does it take to construct a pipeline?
The time it takes to construct a pipeline can vary widely based on several factors. The complexity of the project, the length and diameter of the pipeline, the type of terrain, regulatory approvals, environmental considerations, and unforeseen challenges can all influence the construction timeline. Here are some general considerations:
- Pipeline Type and Purpose:
- The type of pipeline (e.g., oil, gas, water) and its intended purpose (e.g., transportation, distribution) can impact the construction timeline. For example, larger-diameter pipelines or those for long-distance transport may take longer to construct.
- Pipeline Length:
- Longer pipelines typically require more time for construction. The logistics of transporting materials, equipment, and personnel over extended distances can contribute to the overall timeline.
- Terrain and Environment:
- The type of terrain the pipeline traverses can significantly affect construction time. Construction through mountainous or heavily wooded areas may take longer than construction in flat, open terrain. Environmental considerations and regulations may also add time to the planning and approval process.
- Construction Methods:
- The chosen construction methods, whether traditional open trenching, trenchless methods, or a combination, can impact the timeline. Trenchless methods, while minimizing surface disruption, may require more time for planning and execution.
- Regulatory Approvals:
- Obtaining necessary permits and approvals from regulatory authorities can be a time-consuming process. The timeline for securing these approvals varies by location and the complexity of the project.
- Unforeseen Challenges:
- Unexpected issues, such as encountering unforeseen geological obstacles, adverse weather conditions, or community opposition, can lead to delays.
- Project Management and Execution:
- The efficiency of project management and execution by the construction team plays a crucial role. A well-organized and experienced team may be able to complete a project more quickly.
- Testing and Commissioning:
- After the physical construction is complete, testing and commissioning phases may be necessary to ensure the pipeline’s integrity and functionality. The duration of these phases can add to the overall timeline.
Engineering survey for pipeline construction
An engineering survey is a critical component of the planning and design process for pipeline construction. This survey provides accurate and detailed information about the proposed pipeline route, helping engineers make informed decisions and ensuring the successful execution of the project. Here are the key steps involved in an engineering survey for pipeline construction:
- Preliminary Desk Study:
- Gather existing data, maps, and relevant information about the proposed pipeline route.
- Review geological, topographical, and environmental data.
- Route Selection and Feasibility Study:
- Identify potential pipeline routes based on the preliminary desk study.
- Conduct a feasibility study to assess the technical, economic, and environmental viability of each route.
- Consider factors such as terrain, soil conditions, environmental impact, and regulatory requirements.
- Field Reconnaissance:
- Conduct a site visit to visually inspect the proposed pipeline route.
- Identify potential obstacles, landmarks, water bodies, existing infrastructure, and other features that could impact the pipeline construction.
- Topographic Survey:
- Perform a detailed topographic survey to accurately map the terrain along the pipeline route.
- Use surveying instruments such as total stations or GPS to measure elevation, contours, and features of the land.
- Geotechnical Investigation:
- Collect soil and subsurface data through geotechnical investigations.
- Determine soil composition, stability, and other geotechnical parameters to inform trenching and foundation design.
- Boundary and Right-of-Way Survey:
- Establish the legal boundaries of the proposed right-of-way for the pipeline.
- Identify and survey the right-of-way to ensure compliance with property boundaries and regulations.
- Environmental Impact Assessment (EIA):
- Assess the potential environmental impact of the pipeline project.
- Identify sensitive areas, wildlife habitats, and water bodies that may require special consideration.
- Cultural Resource Survey:
- Identify and assess any cultural or historical sites along the pipeline route.
- Ensure compliance with cultural heritage and preservation regulations.
- Utility Location Survey:
- Identify and locate existing utilities (e.g., gas lines, water pipes, electrical cables) within or near the pipeline right-of-way.
- Minimize the risk of interference during construction.
- Alignment Sheets and Profile Drawings:
- Develop alignment sheets and profile drawings that provide detailed information about the pipeline route, including horizontal and vertical alignments.
- Stakeout and Marking:
- Mark the proposed pipeline route on the ground using stakes or markers.
- Ensure the marked route aligns with the surveyed data.
- Data Compilation and Analysis:
- Compile and analyze all collected survey data to create a comprehensive understanding of the pipeline route.
- Use the data to inform the pipeline design, construction plan, and regulatory compliance.
General permits required for pipeline construction
The permits required for pipeline construction can vary depending on the location, type of pipeline, and applicable regulations. It’s essential to engage with regulatory authorities early in the planning process to determine the specific permits needed for your project. Here is a general list of permits commonly required for pipeline construction:
- Environmental Permits:
- Environmental Impact Assessment (EIA): Required to assess and mitigate the potential environmental impact of the pipeline construction.
- Wetland Permits: If the pipeline route involves wetlands, permits may be needed to ensure compliance with wetland protection regulations.
- Water Quality Permits: If the pipeline crosses water bodies, permits may be required to protect water quality during construction.
- Land Use and Zoning Permits:
- Land Use Permits: Ensure compliance with local zoning regulations and land use planning.
- Zoning Variances: If the proposed pipeline deviates from existing zoning regulations, variances may be necessary.
- Right-of-Way and Easement Permits:
- Right-of-Way Permits: Authorize the use of land for the construction and maintenance of the pipeline.
- Easement Agreements: Legal agreements granting the right to use private or public land for the pipeline.
- Construction Permits:
- Construction Permits: Authorize the physical construction activities, including trenching, welding, and installation.
- Grading Permits: If land grading is necessary, a permit may be required.
- Utility and Encroachment Permits:
- Utility Permits: Ensure compliance with regulations related to existing utilities, such as avoiding interference with other underground infrastructure.
- Encroachment Permits: Required for any temporary or permanent encroachments on public rights-of-way.
- Water Appropriation Permits:
- Water Rights Permits: Required if the pipeline construction involves the withdrawal or use of water from natural water sources.
- Air Quality Permits:
- Air Quality Permits: Ensure compliance with regulations related to dust and emissions during construction.
- Cultural Resource Permits:
- Cultural Resource Permits: If archaeological or cultural resources are present, permits may be needed to ensure proper assessment and protection.
- Stormwater Discharge Permits:
- Stormwater Discharge Permits: Required to manage and control stormwater runoff from the construction site.
- Safety and Hazardous Materials Permits:
- Hazardous Materials Permits: If the pipeline involves the transport of hazardous materials, permits may be required for handling, storage, and transportation.
- Safety Permits: Compliance with safety regulations, including permits related to worker safety and emergency response plans.
- Federal Permits:
- S. Army Corps of Engineers (USACE) Permits: Required for activities impacting navigable waters and wetlands.
- Federal Energy Regulatory Commission (FERC) Approval: For interstate natural gas pipelines.
- State and Local Permits:
- State-specific Permits: Many states have their own permitting requirements, which may include additional environmental, safety, or land-use permits.
- Local Municipality Permits: Check with local authorities for any additional permits required within specific municipalities.
Geosynthetics in pipeline construction
Geosynthetics play a significant role in various aspects of pipeline construction, providing solutions to enhance the performance, durability, and environmental sustainability of the infrastructure. Here are some key applications of geosynthetics in pipeline construction:
- Separation and Filtration:
- Geotextiles: Placed between the soil and the pipeline, geotextiles prevent the mixing of soil particles and provide separation. They also act as a filter, allowing water to pass through while preventing the migration of fine particles.
- Erosion Control:
- Geotextiles and Geocells: In areas with challenging terrain or prone to erosion, geotextiles can stabilize the soil, preventing erosion. Geocells, three-dimensional honeycomb structures filled with soil or aggregate, are also used for slope protection and erosion control.
- Pipeline Cushioning:
- Geotextiles and Geocomposites: Placed between the pipeline and the trench, geotextiles or geocomposites can act as a cushioning layer, protecting the pipeline from potential damage during installation and operation.
- Drainage and Filtration:
- Geocomposites: Used for drainage and filtration, geocomposites can provide a protective layer around the pipeline to manage water flow, filter out impurities, and prevent clogging of drainage systems.
- Soil Reinforcement:
- Geogrids and Geotextiles: In areas with weak or unstable soil, geogrids can be used to reinforce the soil and improve its load-bearing capacity. Geotextiles may also be used for soil stabilization.
- Underground Gas and Water Barrier:
- Geomembranes: Used as a barrier to prevent the migration of gases or liquids. Geomembranes can act as a lining to contain fluids and protect the surrounding environment from contamination.
- Slope Stability:
- Geosynthetic Reinforced Soil (GRS): GRS systems use geogrids or geotextiles to reinforce soil, creating stable slopes for embankments and ensuring long-term stability.
- Pipeline Rehabilitation:
- Cured-in-Place Pipe (CIPP) Liners: Geotextiles impregnated with resin are used in trenchless rehabilitation methods. The liner is inserted into an existing pipeline, inflated, and then cured to create a new, structurally sound pipeline within the old one.
- Temporary Access Roads:
- Geotextiles: Placed on the ground surface, geotextiles can provide stabilization and reinforcement for temporary access roads used during pipeline construction, reducing environmental impact.
- Environmental Protection:
- Erosion Control Blankets: Used in environmentally sensitive areas, erosion control blankets made of geotextiles can stabilize soil and prevent erosion until vegetation is established.
- Dewatering:
- Geotextile Dewatering Tubes: Used in dewatering operations, these tubes filled with sediment-laden water are constructed using geotextiles. Water passes through the fabric, leaving the sediment behind.