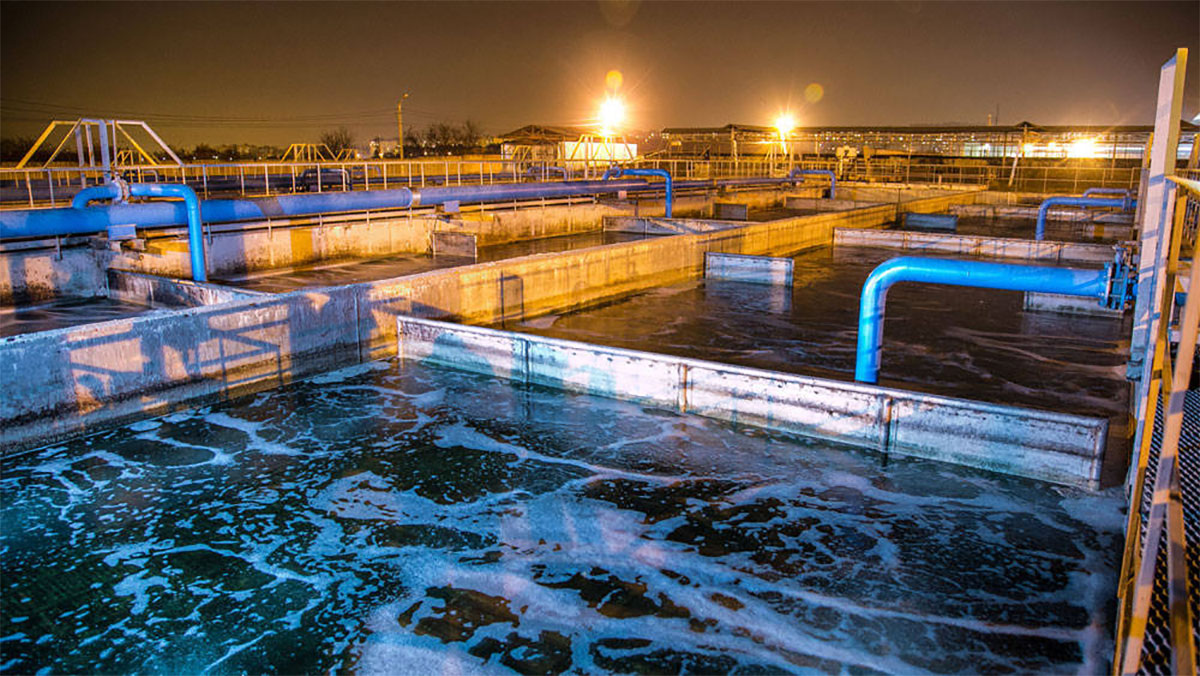
Methods range from gravity and vacuum filtration to membrane processes, with geotextiles playing a significant role in soil stabilization and erosion control. The choice of filtration method depends on the specific engineering requirements and characteristics of the materials involved.
What is filtration in engineering?
Filtration in engineering refers to the process of separating solids or other suspended particles from a fluid (liquid or gas) by passing the fluid through a porous medium or filter. The purpose of filtration is to remove impurities, contaminants, or unwanted particles from the fluid, improving its quality or making it suitable for a specific application. Filtration is a common unit operation in various industries, including chemical processing, water treatment, oil and gas, pharmaceuticals, food and beverage, and many others.
The basic mechanisms of filtration in civil engineering
In civil engineering, filtration typically involves the movement of water through soil to separate and retain particles, with the goal of preventing soil erosion or stabilizing structures. There are two primary mechanisms of filtration in civil engineering:
Grain-to-Grain Contact (Granular Filtration):
In granular filtration, the movement of water through the void spaces between soil particles plays a crucial role. The basic mechanism involves the interlocking of soil particles, forming a natural filter. As water flows through the soil, the particles act as a barrier, allowing water to pass while retaining suspended particles. This process is influenced by factors such as particle size, gradation, and compaction of the soil.
- Particle Size: Smaller particles may be more easily transported by water, while larger particles tend to settle or remain in place.
- Gradation: The distribution of particle sizes in the soil affects the arrangement of void spaces and, consequently, the efficiency of the natural filtration process.
- Compaction: The density and arrangement of soil particles due to compaction influence the permeability of the soil and, consequently, its filtration characteristics.
Geotextile Filtration:
Geotextiles are synthetic fabrics designed to perform specific functions in civil engineering applications. In filtration, geotextiles are used to create a barrier that allows water to pass through while retaining soil particles. This is particularly useful in preventing soil erosion, enhancing drainage, and providing stability to structures.
- Separation: Geotextiles can be placed between different soil layers to prevent the mixing of fine and coarse particles, maintaining the integrity and performance of each layer.
- Drainage: Geotextiles can be employed in drainage systems to facilitate the flow of water while preventing the migration of soil particles.
- Erosion Control: Geotextiles can be used in erosion control applications, such as along riverbanks or slopes, to stabilize the soil and prevent the loss of soil particles due to water flow.
What materials are used in filtration?
Materials used in filtration can vary depending on the specific application, the nature of the particles being filtered, and the desired level of filtration. Here are some common materials used in filtration:
- Filter Media:
- Sand: Used in slow sand filters and rapid sand filters for water treatment. Sand filtration relies on the size and shape of sand particles to trap impurities.
- Activated Carbon: Effective in adsorbing organic compounds and some chemicals. It is commonly used in water and air purification.
- Diatomaceous Earth: A porous material formed from the fossilized remains of diatoms. It is used as a filter aid in various industries, including food and beverage processing and swimming pool filtration.
- Cellulose and Paper: Used in various filters, including some automotive air filters and laboratory filtration.
- Fiberglass: Commonly used in high-efficiency particulate air (HEPA) filters for air purification applications.
- Polypropylene and Polyester: Synthetic materials used in membrane filtration and various types of cartridge filters.
- Metal Screens: Used for sieving and filtering larger particles. Stainless steel and other metals may be employed in industrial applications.
- Geotextiles:
- Polypropylene: Commonly used in geotextiles for civil engineering applications, providing separation, filtration, and reinforcement in soil and drainage systems.
- Polyester: Used in geotextiles for applications where greater strength and resistance to environmental conditions are required.
- Polymeric Membranes (Polyethersulfone, Polyamide, Polysulfone): Used in microfiltration, ultrafiltration, nanofiltration, and reverse osmosis processes for water and wastewater treatment, as well as in pharmaceutical and biotechnological applications.
- Ceramic Membranes: Known for their durability and resistance to high temperatures and chemicals, used in various filtration processes.
- Stainless Steel: Used in industrial applications where a durable and corrosion-resistant filter medium is required.
- Mixed-Matrix Membranes: Combining polymers with inorganic materials to enhance the performance and selectivity of membranes in various filtration processes.
- Cotton: Used in some medical and laboratory filters due to its natural ability to trap particles.
- Membranes:
- Metallic Filters:
- Composite Materials:
- Natural Fibers:
What are the types of filtration in engineering?
In engineering, filtration is a common process used to separate solids or other unwanted particles from fluids (liquids or gases). There are several types of filtration, each with its own mechanism and application. Here are some of the common types of filtration in engineering:
- Gravity Filtration:
- Mechanism: The fluid is allowed to flow through a porous medium under the influence of gravity.
- Application: Commonly used in laboratory settings and small-scale processes.
- Vacuum Filtration
- Mechanism: A vacuum is applied to enhance the flow of fluid through the filter medium.
- Application: Widely used in laboratory and industrial settings, particularly when faster filtration is required.
- Mechanism: Fluid is forced through a filter medium under the influence of pressure.
- Application: Used in various industrial processes where a higher filtration rate is needed.
- Mechanism: Particles are separated from the fluid due to centrifugal force generated by rotating the filtration system.
- Application: Common in industries such as oil and gas, where high-speed rotation helps separate solids from liquids.
- Mechanism: Uses membranes with relatively large pore sizes to separate particles from the fluid.
- Application: Common in pharmaceutical and biotechnological processes, as well as water treatment.
- Mechanism: Utilizes membranes with smaller pore sizes than microfiltration, allowing the separation of smaller particles and macromolecules.
- Application: Used in various industrial processes, including the food and beverage industry and wastewater treatment.
- Mechanism: Employs membranes with even smaller pore sizes, allowing the separation of ions and smaller molecules.
- Application: Common in water treatment and certain industrial applications requiring precise separation.
- Mechanism: Involves the use of a semi-permeable membrane to separate solute from solvent under pressure.
- Application: Widely used for desalination of seawater, water purification, and in some industrial processes.
- Mechanism: Involves passing the fluid through a thick layer of porous material to trap particles throughout the depth of the filter medium.
- Application: Common in air and water filtration systems.
- Mechanism: Uses a screen or mesh to separate particles based on their size.
- Application: Common in various industries for removing larger particles from fluids.
- Mechanism: Involves the continuous movement of fluid parallel to the filter surface, reducing the accumulation of particles and improving efficiency.
- Application: Used in membrane filtration processes to minimize fouling and maintain a consistent flow.
- Pressure Filtration
- Centrifugal Filtration
- Microfiltration
- Ultrafiltration
- Nanofiltration
- Reverse Osmosis
- Depth Filtration
- Screen Filtration
- Crossflow Filtration
Filtration using geotextiles
Filtration using geotextiles is a common technique in civil engineering and environmental applications. Geotextiles are synthetic or natural fabrics specifically designed for use in soil, rock, or other geotechnical engineering applications. They serve various functions, including separation, filtration, drainage, and reinforcement. When it comes to filtration, geotextiles act as a barrier that allows water to pass through while retaining soil particles. Here’s how filtration using geotextiles works:
- Separation:
- Geotextiles are often used to separate different soil layers with distinct particle sizes and properties. For example, a geotextile may be placed between a fine-grained soil layer and a coarse-grained soil layer to prevent mixing and maintain the integrity of each layer.
- Filtration:
- Geotextiles act as filters by allowing water to pass through while preventing the movement of soil particles. When water flows through the soil, the geotextile retains fine particles, preventing them from being washed away. This is particularly important in erosion control applications.
- Geotextiles are used in drainage systems to facilitate the flow of water while preventing the migration of soil particles. They are often incorporated into geocomposite drainage systems to provide both filtration and drainage functions.
- Geotextiles are deployed in erosion control applications, such as along riverbanks, slopes, or construction sites. They stabilize the soil by preventing the loss of fine particles, reducing erosion caused by water flow.
- Drainage
- Erosion Control
The effectiveness of geotextile filtration depends on factors such as the type of geotextile used, its pore size, permeability, and the characteristics of the soil and water involved. There are different types of geotextiles with varying properties, such as woven geotextiles, non-woven geotextiles, and geocomposites.
Key considerations in filtration using geotextiles:
- Pore Size: The pore size of the geotextile should be selected based on the soil type and the desired level of filtration. It determines the size of particles that can pass through.
- Permeability: The permeability of the geotextile influences the flow of water through the fabric. It is essential to balance filtration efficiency with drainage requirements.
- Installation: Proper installation of geotextiles is crucial for their effectiveness. They need to be correctly placed to ensure optimal separation and filtration.
Conclusion
Filtration in engineering involves separating particles from fluids using various methods such as gravity, vacuum, pressure, or membranes. In civil engineering, geotextiles are commonly employed for filtration, aiding in soil separation, erosion control, and drainage. The choice of filtration method depends on factors like particle size, application requirements, and the characteristics of the fluid or soil involved.