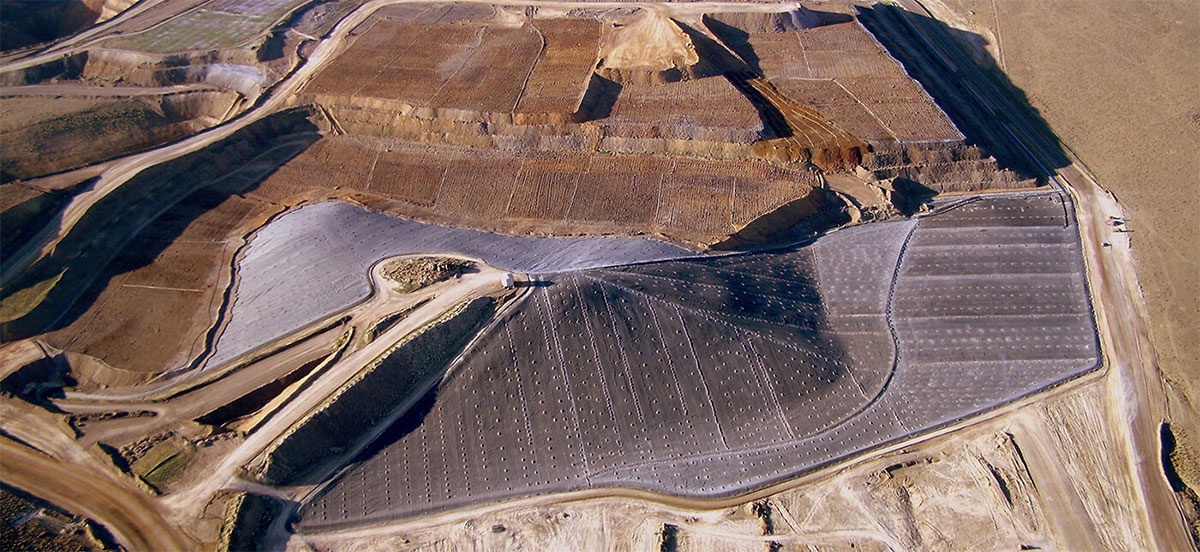
Choosing the right mining geomembranes is essential to ensure effective containment of hazardous materials, environmental stewardship, and operational efficiency. This selection process involves considering various factors, including material properties, site conditions, and regulatory requirements, to mitigate risks and achieve project objectives.
What are the preferred geomembranes for mining projects?
In mining projects, the appropriate mining geomembranes often depend on various factors such as the specific requirements of the project, environmental considerations, site conditions, and regulatory standards. However, some common geomembranes used in mining projects include:
- High-Density Polyethylene (HDPE): HDPE geomembranes are popular in mining projects due to their excellent chemical resistance, durability, and puncture resistance. They are effective for lining tailings ponds, heap leach pads, and other containment areas.
- Linear Low-Density Polyethylene (LLDPE): LLDPE geomembranes offer similar characteristics to HDPE but with improved flexibility, making them suitable for applications where differential settlement or movement is expected.
- Polyvinyl Chloride (PVC): PVC geomembranes are known for their chemical resistance and flexibility. They are often used in mining projects for applications such as lining ponds, reservoirs, and wastewater containment.
- Ethylene Propylene Diene Monomer (EPDM): EPDM geomembranes are synthetic rubber liners known for their elasticity, UV resistance, and durability. They are commonly used in mining projects for lining applications where flexibility and resistance to weathering are essential.
- Reinforced Polyethylene (RPE): RPE geomembranes combine the advantages of HDPE with added reinforcement for increased strength and puncture resistance. They are suitable for lining applications in harsh mining environments.
Mining geomembrane selection: The best material
Determining the “best” material for mining geomembranes depends on various factors specific to each project, including environmental conditions, the type of materials being contained, durability requirements, regulatory standards, and budget constraints. However, High-Density Polyethylene (HDPE) geomembranes are often considered one of the top choices for many mining applications due to their versatility and excellent performance characteristics:
- Chemical Resistance: HDPE geomembranes have high chemical resistance, making them suitable for containing acidic or alkaline substances commonly found in mining operations, such as leachates from heap leach pads or tailings ponds.
- Durability: HDPE geomembranes offer excellent puncture resistance, tear resistance, and UV stability, ensuring long-term performance even in harsh mining environments.
- Weldability: HDPE geomembranes can be heat-welded to create seamless liners, minimizing the risk of leaks and ensuring integrity in containment systems.
- Cost-Effectiveness: HDPE geomembranes typically offer a good balance between performance and cost, making them a cost-effective solution for many mining projects.
- Environmental Compatibility: HDPE geomembranes are inert and have minimal environmental impact, meeting regulatory standards for environmental protection in mining applications.
The appropriate thickness for geomembranes in the mining industry
The appropriate thickness for geomembranes in the mining industry depends on several factors, including the specific application, site conditions, environmental considerations, regulatory requirements, and engineering design considerations. Here’s what you need to consider:
1. Application:
- Leach pads: Typically use 1.5mm to 2.0mm HDPE or LLDPE with an additional protective layer like geotextile.
- Tailings ponds: Often require thicker liners, ranging from 1.5mm to 2.0mm with double liners becoming increasingly common.
- Heap leach pads: May use thinner liners (1.0mm) for temporary covers, but exposed areas typically require 1.5mm to 2.0mm HDPE.
- Run-of-mine dumps: Traditionally unlined, but geomembranes are gaining traction, with thicknesses similar to leach pads.
2. Material properties:
- Tensile strength and elongation: Thicker liners offer better resistance to stretching and tearing.
- Puncture resistance: Crucial for applications with sharp-edged materials like rocks or debris. Thicker liners offer better protection.
- Chemical resistance: Consider the specific chemicals involved in the mining process and choose a material with adequate resistance.
3. Regulatory requirements:
- Local regulations may dictate minimum thicknesses for geomembranes in different applications. Ensure your chosen thickness complies with relevant standards.
4. Project budget:
- Thicker liners offer enhanced performance but come at a higher cost. Weigh the benefits against project budget constraints.
5. Expertise of consultants:
- Consulting with geotechnical engineers and experienced mining professionals can provide valuable insights into the optimal thickness for your specific project.
General recommendations:
- 1.5mm to 2.0mm HDPE or LLDPE: This is the most common range for various mining applications, offering a good balance of performance and cost.
- Consider thicker options (2.0mm+) for: Demanding applications with high pressure, sharp materials, or aggressive chemicals.
- Seek professional advice: Consulting with experts can ensure you select the most appropriate thickness for your specific needs.
Color selection for geomembranes used in mining
The color selection for geomembranes used in mining projects can depend on various factors, including functionality, environmental considerations, safety, and regulatory requirements. While geomembranes are commonly available in black due to its UV resistance and heat absorption properties, other colors may be used for specific purposes. Here’s a breakdown of color considerations for geomembranes in mining:
- Black:
- UV Resistance: Black geomembranes are often preferred for outdoor applications in mining projects due to their superior UV resistance, which helps prevent degradation over time.
- Heat Absorption: Black geomembranes absorb more heat than lighter colors, which can be advantageous in colder climates to prevent freezing or maintain temperature-sensitive processes.
- White or Light Colors:
- Solar Reflectivity: Light-colored geomembranes reflect more solar radiation, reducing heat absorption and potential temperature fluctuations within containment areas. This can be beneficial for mitigating temperature-sensitive processes or minimizing heat buildup in warmer climates.
- Visibility: Light-colored geomembranes can enhance visibility within containment areas, making it easier to detect leaks or monitor operations.
- Other Colors (e.g., Blue, Green):
- Aesthetics: Colored geomembranes may be chosen for aesthetic reasons or to blend in with the surrounding landscape, especially in environmentally sensitive areas or where visual impact is a concern.
- Differentiation: Using different colors for geomembranes in multi-layer liner systems can help differentiate between layers during installation and inspection.
- Regulatory and Safety Considerations:
- Some regulatory agencies or safety standards may specify color requirements for geomembranes in mining projects to denote specific functions (e.g., identifying hazardous materials, delineating different zones within the site) or to ensure compliance with visibility and safety regulations.
Mining geomembrane sheet safety
Ensuring safety when using geomembrane sheets in mining projects is paramount to protect workers, the environment, and surrounding communities. Here are some key safety considerations:
- Material Handling: Geomembrane sheets can be heavy and cumbersome to handle, especially in large rolls. Proper lifting techniques, equipment, and personal protective equipment (PPE) should be used to prevent injuries during handling and installation.
- Installation Safety: Installing geomembranes often involves working near excavation sites, slopes, or bodies of water. Workers should be trained in excavation and trenching safety, fall protection, and confined space entry if applicable. Additionally, proper anchoring and securing of geomembrane sheets are essential to prevent displacement or accidents.
- Chemical Exposure: In mining applications, geomembranes may come into contact with hazardous chemicals, acids, or leachates. Workers should be trained in chemical handling and wear appropriate PPE, including gloves, goggles, and respiratory protection, when working with or near potentially hazardous substances.
- Fire Safety: Some geomembrane materials may be combustible or emit toxic fumes when exposed to fire. Fire prevention measures, such as fire-resistant barriers and firefighting equipment, should be in place to mitigate the risk of fires and ensure worker safety.
- Environmental Protection: Geomembranes are used to contain potentially harmful substances such as mine tailings or process solutions. Proper containment and leak detection systems should be in place to prevent environmental contamination and mitigate the risk of leaks or spills.
- Training and Education: Workers involved in handling, installing, and maintaining geomembrane liners should receive adequate training in safety protocols, emergency procedures, and hazard recognition. Regular safety meetings and refresher training sessions can help reinforce safe work practices.
- Regulatory Compliance: Mining operations are subject to regulatory standards and guidelines governing workplace safety, environmental protection, and hazardous materials handling. Compliance with relevant regulations and industry best practices is essential to ensure a safe working environment and prevent accidents or regulatory violations.
Mining geomembranes price
The price of mining geomembranes can vary depending on a number of factors, including:
- Material: The most common type of mining geomembrane is high-density polyethylene (HDPE), but other materials such as PVC and EPDM are also used. HDPE is generally the most affordable option, while EPDM is more expensive but offers better chemical resistance.
- Thickness: Thicker geomembranes are more durable and resistant to damage, but they are also more expensive. The thickness you need will depend on the specific application.
- Size: Larger geomembranes are more expensive than smaller ones.
- Quantity: Suppliers often offer discounts for larger orders.
- Market demand and availability: The price of geomembranes can fluctuate depending on supply and demand.
Based on these factors, the price of mining geomembranes can range from US$0.34 to US$2.31 per square meter.
Here are some additional factors that can affect the price of mining geomembranes:
- Shipping costs: The cost of shipping geomembranes can vary depending on the location of the supplier and the buyer.
- Customs duties and import taxes: These can add to the cost of geomembranes if they are imported from another country.
- Installation costs: The cost of installing geomembranes can vary depending on the size and complexity of the project.
Conclusion
In conclusion, selecting the appropriate mining geomembranes is crucial for ensuring containment integrity, environmental protection, and worker safety. Factors such as material properties, thickness, chemical resistance, and regulatory compliance must be carefully considered to mitigate risks and achieve long-term performance in challenging mining environments.